جوشکاری Welding
جوشکاری
فهرست مطالب
جوشکاری چیست؟
جوش به معناي پيوستگي و اتصال در يك ماده ميباشد. جوشکاری يكي از فرآيندهاي اتصال حرارتي قطعات (فلزي يا غيرفلزي)، به روش ذوبي يا غير ذوبي، با بهكارگيري يا بدون بهكارگيري فشار و با استفاده از ماده پركننده مي باشد. انواع فرآيندهاي جوشکاری به دو دسته اصلي تقسيم ميشوند: فرآيندهاي جوشکاری ذوبي و فرآيندهاي جوشکاری غيرذوبي. جوشکاری يكي از روش هاي توليد ميباشد. هدف آن اتصال دايمي مواد مهندسي از قبيل فلز، سراميك، پليمر، كامپوزيت و غيره به يك ديگر است.
به گونه اي كه خواص اتصال، برابر خواص ماده پايه باشد. در يك جوشکاری ايدهآل، پيوستگي كامل بين اجزاي يك اتصال به وجود ميآيد.
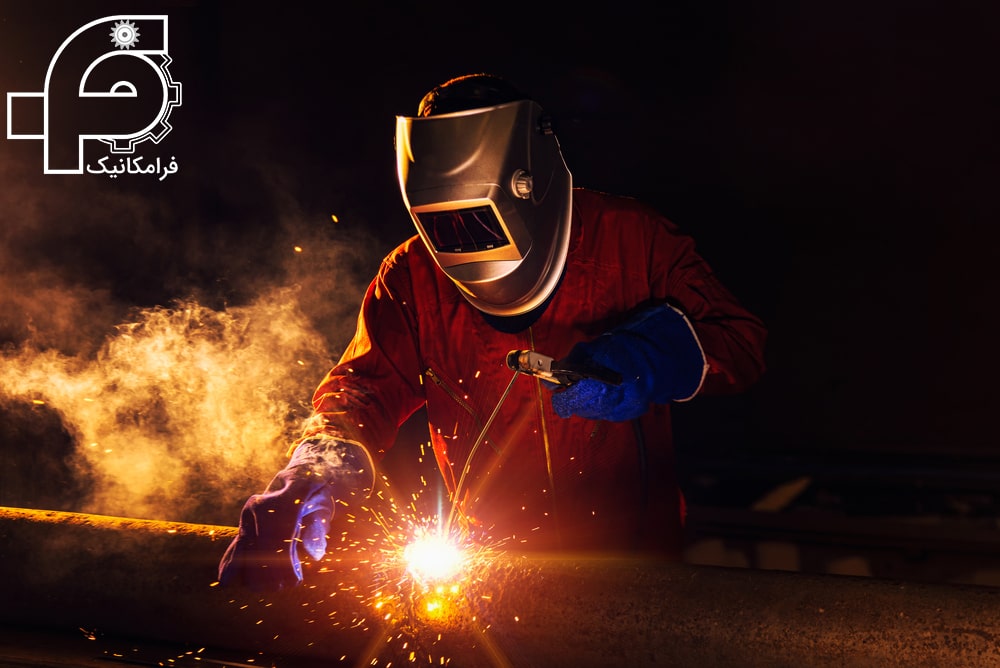
جوشکاری را ميتوان اتصال دايم متالورژيكي دانست كه ميتواند در حالت مذاب يا جامد، با استفاده مواد پركننده يا بدون واسطه و با ايجاد فشار يا بدون استفاده از فشار صورت گيرد. در واقع جوشکاری به اتصالي گفته ميشود كه نتوان محل اتصال را از قسمتهاي ديگر قطعات جدا نمود و به عبارتي ديگر خواص جوش ايجاد شده با قطعات مورد اتصال يكسان يا نزديك به هم باشد.
تاريخچه پیدایش جوش
پيشينه استفاده از اولين فرآيند جوشکاری به زماني برميگردد كه بشر براي ساخت يك سلاح ابتدايي از يك نوع اوليه اين فرآيند استفاده ميكرد. جوشکاری آهنگري قديميترين فرآيند جوشکاری ميباشد، كه انسان قطعات فلز را به صورت سرد يا گداخته بر روي يكديگر قرار داده و در اثر كوبيدن موجب اتصال آنها ميشد. در سال 1856 دانشمندي به نام ژول (Joule) به فكر جوشکاری مقاومتي افتاد و بعد از او اليهو تامسون (Elihu Thomson) آمريكایي در بين سالهاي 1876 تا 1877 به طرحهاي او جامه عمل پوشاند و از جوشکاری مقاومتي استفاده كرد.
اما زمان پيدايش قوس الكتريكي به سال 1802، زماني كه دانشمندي روسي به نام واسيلي پتروف (Vasily Petrov) پي برد كه اگر دو تكه زغال چوب را به قطبهاي باتري بزرگي وصل كنيم و آنها را به هم تماس دهيم و سپس كمي از هم جدا كنيم شعله روشني بين دو تكه زغال ديده ميشود. انتهاي آنها كه از شدت گرما سفيد شده است نور خيره كنندهاي گسيل ميدارد.
ادامه
در سال 1886 يك دانشمندان روسي بنام بناردوز (Nikolai Benardos) اختراعي را به ثبت رساند كه به وسيله آن قادر بود تا يك قطعه فلزي را با الكترود زغالي به صورت موضعي با ايجاد قوس الكتريكي بين قطعه و الكترود ذوب نمايد. بناردوز در اين روش دو قطعه فلزي را در فاصله مشخص از يكديگر قرار داده و با استفاده از پديده قوس و حركت الكترود زغالي در طول شكاف بين دو قطعه و وارد نمودن همزمان ميلهاي فلزي از جنس قطعه در داخل قوس الكتريكي، حمام مذابي به وجود آورد كه بعد از منجمد شدن شكاف موجود را پر نموده و باعث به هم پيوستن اين قطعات گرديد.
تکامل
در سال 1888 دانشمند ديگر روسي بنام اسلاويانوف (Nikolai Slavyanov)، روش الكترود ذوبشونده را اختراع نمود. او در اين روش الكترود فلزي را جايگزين الكترود زغالي كرد كه همزمان علاوه بر ايجاد قوس، وظيفه فلز پركننده را نيز به عهده داشت. در روش الكترود ذوبشونده مذاب حاصل از الكترود فلزي در فاصله بين نوك الكترود و شكاف دو قطعه در معرض هوا قرار ميگرفت كه اين امر باعث اكسيده شدن مذاب و در نتيجه ايجاد اشكال در جوش ميگرديد. از طرف ديگر قوس الكتريكي به دليل تماس با اتمسفر هوا نيز ناپايدار بوده كه خود به خود غير يكنواختي جوش را به دنبال داشت.
براي برطرف نمودن عيوبي مانند كيفيت پايين فلز جوش از لحاظ مكانيكي و اكسيد شدن آن و همچنين ناپايداري قوس در سال 1905 يك صنعتگر سوئدي بنام اسكار كژلبرگ (Oscar Kjellberg) الكترود فلزي پوششدار را اختراع نمود. پوشش اين الكترود را مخلوطي از مواد معدني مختلف از جمله آهك تشكيل ميداد كه بهوسيله توليد گاز و ايجاد سرباره، قادر به محافظت از مذاب حاصل از ذوب الكترود در مقابل آثار نامطلوب در تماس با هوا بود. علاوه بر اين، پوشش الكترود باعث پايداري قوس الكتريكي و يكنواختشدن جوش ميگرديد.
اختراعات
پس از سال 1905 با اختراع الكترود پوششدار، صنعت اين امكان را يافت تا جوشهايي با استحكام معادل فلز پايه بهوجود آورد. در جريان جنگ هاي جهاني اول و دوم، جوشکاری پيشرفت زيادي كرد. احتياجات بشر به اتصالات مدرن، سبك، محكم و مقاوم در سالهاي اخير و مخصوصاً بيست سال اخير، سبب توسعه سريع اين فناوري شده است. در سال 1930 به طور همزمان در آمريكا و اتحاد جماهير شوروي سابق، تحقيقاتي براي مخفي ساختن قوس الكتريكي و دستيابي به قوسي پايدار صورت گرفت كه نتيجه آن اختراع جوشکاری زير پودري بود اما نه به شكل امروزي بلكه با استفاده از الكترودهاي كربني.
حدود سال 1935 اين روش تقريبا به شكل امروزي خود درآمد و تبديل به روشي مناسب از لحاظ اقتصادي براي جوشکاری شد. در جنگ جهاني اول پس از جوش خوردن تركشهاي ناشي از متلاشي شدن گلوله توپ به بدنه جنگ افزارها فرآيند جوشکاری انفجاري كشف شد. سال 1950 به طور همزمان در كشورهاي آمريكا و آلمان غربي جوشکاری پرتو الكتروني (EBW) توسعه يافت.
کم و بیش در سال 1965 سيستمهاي متنوع ليزري به منظور جوشهاي مدارهاي الكتريكي و داخل محفظههاي خلاء و همچنين در ساير كاربردهاي تخصصي كه در آنها تكنولوژيهاي مرسوم قادر به ايجاد اتصالات مطمئن نبودند، توسعه داده شد.
جدیدترین روش
شايد بتوان گفت جديدترين روش جوشکاری، فرآيند جوشکاری اصطكاكي اغتشاشي باشد. جوشکاری اصطكاكي اغتشاشي براي اولين بار براي آلياژهاي آلومينيوم ابداع گشت و يك روش جوشکاری در حالت جامد است. اين روش در سال 1991 توسط انستيتو جهاني جوش و اتصالات (TWI) در كمبريج تحت عنوان روش جوشکاری تحريكي اصطكاكي(Friction Stir Welding ) به صنعت دنيا معرفي شد.
انواع فرآيندهاي جوشکاری
در يك تقسيم بندي كلي، پديده اتصال حرارتي به فرآيندهاي زير، تقسيم بندي ميشود:
- جوشکاری با پرتوي الكتروني
- لحيم كاري سخت در كوره Furnace Brazing
- جوشکاری قوس الكتريكي با گاز محافظ (MIG)
- لحيم كاري سخت با شعله Gas torch braze welding
- جوشکاری قوس تنگستن با گاز محافظ (TIG)
- جوشکاری با پرتوي ليزر Laser Beam Welding
- لحيم كاري غوطهوري Metal bath dip soldering
- جوشکاری با قوس پلاسما Plasma Arc Welding
- نقطه جوش برجسته Projection Welding
- جوشکاری با قوس الكتريكي و الكترود پوششدار Shielded Metal Arc Welding
- نقطه جوش Spot Welding
- جوشکاری زيرپودري Submerged Arc Welding
- لحيم كاري مدارات الكترونيكي Wave Soldering
با توجه به اين طبقه بندي، در زير به بررسي اجمالي هر يك از اين فرآيندها ميپردازيم:
جوشکاری با پرتوي الكتروني
جوشکاری با پرتوي الكتروني يكي از فرآيندهاي اتصال قطعات فلزي است كه در آن حرارت مورد نياز براي ذوب كردن موضعي قطعه كار از طريق تابش يك پرتوي پر سرعت و متمركز از الكترونها تامين ميشود. در اثر برخورد الكترونها به قطعه كار، انرژي جنبشي آنها به گرما تبديل ميگردد. در اين عمليات عموما از سيم جوش يا فيلر (پركننده) استفاده نميشود.
ويژگيهاي فرآيند جوش پرتو الکترونی
- در اين فرآيند بايد يك محفظه خلاء وجود داشته باشد
- در اين فرآيند نيازي به استفاده از سيمجوش نيست
- پس از اين فرآيند اعوجاج كمي در قطعه كار ايجاد ميشود
- نفوذ جوش در اين فرآيند عالي است
- به سادگي قابليت اتوماسيون را داراست
- ناحيه جوش باريكي را ايجاد ميكند
- حرارت در ناحيه جوش خيلي زياد است، ولي نواحي متاثر از حرارت بسيار كوچك هستند
قابليتهاي فرآيند
عليرغم محدوديتهاي مطرح شده، روش جوشکاری با پرتوي الكتروني قابليتهاي زيادي دارد. در اين فرآيند، شيار جوشکاری باريكي ايجاد ميشود و نيازي به سيم جوش ندارد. با اين روش ميتوان قطعاتي با ضخامت 0.3 تا 2 اينچ را جوشکاری نمود.
پهناي جوش در اين روش معمولا از 0.001 تا 0.01 اينچ ميباشد.
محدوديتهاي فرآيند
با توجه به لزوم استفاده از محفظه خلاء، محدوديت هايي در جوشکاری با اين روش به وجود ميآيد. يكي از محدوديت ها اين است كه بايد بتوان قطعه را در داخل محفظه جاي داد. محدوديت ديگر، تنظيم دقيق موضع جوشکاری در زير پرتو ميباشد.
محدوديت كنترل قطعه در هنگام جوشکاری نيز از ديگر محدوديت ها ميباشد.
عيوب جوشکاری
در اين جوشکاری گاهي اوقات حفره و تنشهاي داخلي به وجود ميآيد. به جدول زير توجه نماييد:
جدول 1- عيوب جوشکاری با پرتوي الكتروني
اثرات | علل احتمالي | نوع عيب |
كاهش استحكام جوش | سرعت زياد جوشکاری ، تمركز ضعيف پرتو، توان ناكافي، پهناي زياد شيار جوشکاری. | حفره |
كاهش استحكام جوش، اعوجاج و پيچيدگي قطعه | سرعت كم جوشکاری، تمركز ضعيف پرتو، توان بيش از حد. | تنشهاي داخلي |
اثرات جوشکاری با پرتوي الكتروني
اين روش جوشکاری اثرات اندكي بر خواص مختلف قطعه كار ميگذارد كه در جدول زير ارايه شده است:
جدول 2- اثرات جوشکاری با پرتوي الكتروني بر خواص ماده
اثرات جوشکاری با پرتوي الكتروني بر خواص ماده | خواص ماده |
اختمال سخت شدن يا نرم شدن موضع جوشکاری | مكانيكي |
اثري ندارد | فيزيكي |
اثري ندارد | شيميايي |
جنس قطعه كار
در جدول زير، قابليت جوشکاری مواد مختلف به روش پرتوي الكتروني ارايه شده است:
جدول 3- قابليت جوشکاری مواد مختلف به روش پرتوي الكتروني
جنس قطعه كار | قابليت جوشکاری | ||||||||||||||
ضعيف | متوسط | خوب | عالي | ||||||||||||
آلومينيوم | ****** | ************** | ******* | ||||||||||||
فولاد | ************** | ************** | ***** | ||||||||||||
فولاد زنگ نزن | ************** | ************** | *** | ||||||||||||
تانتال | ************* | ************ | ********* | ||||||||||||
تنگستن | ********** | *********** | ******** | ||||||||||||
مس | ************* | ********* | ********* | ||||||||||||
*: محدوده معمول | *: محدوده ممكن | ||||||||||||||
لحيم كاري سخت در كوره
لحيم كاري سخت در كوره، يكي از فرآيندهاي اتصال قطعات و جوشکاری است كه در آن از سيم جوش يا ماده پركننده براي اتصال دو قطعه به هم استفاده ميشود. حرارت داخل كوره، سيم جوش را ذوب كرده و آن را در محل اتصال جاري ميسازد. با توجه به خاصيت مويينگي، فلز ذوبشده به شيارهاي باريك محل اتصال نيز نفوذ خواهد كرد.
ويژگيهاي فرآيند
- از حرارت داخل كوره براي گرم كردن قطعه كار و ذوب سيم جوش استفاده ميشود.
- دماي داخل كوره بايد به اندازهاي باشد كه فقط سيم جوش را ذوب كند
- در اين فرآيند ميتوان همزمان چند اتصال را لحيم كاري نمود.
قابليتهاي فرآيند
براي انجام يك لحيم كاري سخت موفق، در داخل كوره، بايد سيم جوش و فلاكس را به درستي در محل درز جوش توزيع نمود. اندازه قطعاتي كه به اين روش لحيم كاري ميشوند از 8 تا 125 اينچ مكعب تغيير ميكنند. ضخامت قطعه كار نيز معمولا بين 0.2 تا 0.8 اينچ ميباشد.
اثرات لحيم كاري سخت در كوره بر خواص مواد
اين فرآيند ممكن است باعث سخت شدن، ترد شدن و كاهش استحكام ماده اصلي شود.
جدول 4- اثرات لحيمكاري سخت در كوره بر خواص مواد
اثرات لحيم كاري سخت در كوره بر خواص مواد | خواص ماده |
سخت شدن، ترد شدن و كاهش استحكام | مكانيكي |
احتمال تغيير ابعادي و ساختاري | فيزيكي |
اثرات اندكي دارد | شيميايي |
انواع سيم جوش
در جدول زير سيم جوشهاي مناسب براي لحيم كاري سخت مواد مختلف، بر اساس كدگذاري انجمن جوش آمريكا (AWS) به همراه دماي مناسب جهت لحيمكاري، داده شده است:
جدول 5- انواع سيم جوش
ماده اصلي كار | نوع سيمجوش | دماي لحيم كاري سخت (فارنهايت) |
آلومينيوم | BAlSi-3 | 1060-1120 |
مس | BCuP-3 | 1300-1500 |
نقره | BAg-6 | 1425-1600 |
طلا | BAu-2 | 1635-1850 |
نيكل | BNi-4 | 1850-2150 |
جوشکاری قوس الكتريكي با گاز محافظ (MIG)
اين نوع جوشکاری GMAW مخفف عبارت Gas Metal Arc Welding، يك روش جوشکاری با قوس الكتريكي است كه الكترود مصرف شدني داشته و پوششي از يك گاز خنثي، محفظه جوشکاری را حفاظت ميكند. واژه MIG از عبارت Metal Inert Gas گرفته شده است.
ويژگيهاي فرآيند
- در اين فرآيند، الكترود علاوه بر ايجاد قوس الكتريكي، به عنوان سيم جوش ذوب شده و درز جوش را پر ميكند،
- پوششي از گاز محافظ در اين روش استفاده ميشود،
- گرده جوش حاصل، يكنواخت است،
- در اين عمليات، گل جوش به وجود نميآيد،
- اين فرآيند معمولا براي جوشکاری اتوماتيك مورد استفاده قرار ميگيرد.
ماشين و تجهيزات
تجهيزات مورد نياز در اين روش عبارتند از:
- يك ماشين جوشکاری كه جريان الكتريكي قابل تنظيم براي الكترود را تامين ميكند
- يك مكانيزم جلوبرنده سيم جوش كه الكترود را با سرعت قابل تنظيم هدايت ميكند
- يك تفنگ جوشکاری كه در دست اپراتور قرار دارد و سيم جوش از داخل آن به طرف موضع جوش رانده ميشود
- كپسول گاز محافظ كه آرگون و هليم از در دسترسترين اين گازها ميباشند. دياكسيدكربن نيز به دليل قيمت مناسب، در اين روش كاربرد زيادي دارد.
قابليتهاي فرآيند
در صورتي كه فضاي كافي جهت هدايت و حركت تفنگ جوشکاری وجود داشته باشد، تقريبا هر فرم اتصالي را ميتوان با اين روش، جوشکاری نمود. ضخامت قطعاتي كه با اين روش جوشکاری ميشوند، معمولا بين 0.125 تا 1 اينچ ميباشند. در شرايط خاص، اين ضخامت از 20.0 تا 2.5 اينچ متغيير ميباشد.
كيفيت جوشکاری
كيفيت اين نوع جوشکاری، تقريبا مشابه كيفيت ديگر روشهاي جوشکاری با قوس الكتريكي و حتي بهتر است. عيوب ممكن در اين روش، در جدول زير مشاهده ميشود:
جدول 6- عيوب روش جوشکاری MIG
اثرات نامطلوب | علل ممكن | نوع عيب |
كاهش استحكام قطعه، جوشکاری نامطلوب | تنشهاي مكانيكي، تنشهاي حرارتي، وجود ناخالصي در عناصر آلياژي قطعه كار يا سيم جوش | ترك |
كاهش استحكام جوشکاری | ناكافي بودن گاز محافظ، به تله افتادن گاز درون درز جوش | حفره (تخلخل) |
ظاهر بد | جريان بالاي الكتريكي | گرده جوش خشن |
كاهش استحكام استاتيك، احتمال
ايجاد تنش، جوشکاری نامطلوب |
سطوح كثيف قطعه كار، سرعت زياد جوشکاری | عدم ذوب كامل سيم جوش |
انواع گازهاي محافظ
در جدول زير انواع گازهاي محافظ در اين روش و مزايا و ويژگيهاي هريك را مشاهده مينماييد:
جدول 7- انواع گازهاي محافظ، مزايا و ويژگيهاي آنها
ويژگيها و كاربردها | نوع گاز | |
بهترين گاز براي جوشکاری انواع فلزات | – | آرگون |
مناسب براي جوشکاری با جريان الكتريكي پايين | – | |
برقراري آسان قوس الكتريكي، ايجاد قوسي پايدار و يكنواخت | – | |
مناسب براي جوشکاری فولاد نرم، آلومينيوم، تيتانيوم و فولادهاي آلياژي | – | |
امكان برقراري جريان گاز به اندازه 1.5 تا 3 برابر جريان گاز آرگون | – | هليم |
جوشکاری سريع فولاد نرم و تيتانيوم | – | |
ناحيه متاثر از حرارت با استفاده از اين گاز كوچكتر ميشود | – | |
مناسب براي جوشکاری فولاد زنگ نزن و مس | – | |
معمولا به عنوان گاز مخلوط شونده با گازهاي ديگر به كار ميرود | – | دي اكسيدكربن |
مناسب براي جوشکاری فولادهاي كربني و كم آلياژ | – |
اثرات جوشکاری MIG بر خواص ماده
جدول 8- اثرات جوشکاری MIG بر خواص ماده
اثرات جوشکاری MIG بر خواص ماده | خواص ماده |
احتمال سخت شدن قطعه كار، كاهش استحكام خستگي، ايجاد انقباض در قطعه كار، نرم شدن قطعه كار، اعوجاج و پيچيدگي در قطعه كار | مكانيكي |
احتمال افت كيفيت ظاهري و ايجاد ترك و تخلخل | فيزيكي |
احتمال كاهش مقاومت خوردگي در ناحيه جوشکاری شده | شيميايي |
جنس قطعه كار
اغلب فلزات را ميتوان به اين روش جوشکاری نمود. سيمجوش نيز در قابليت جوشکاری مواد مختلف موثر ميباشد. بنابراين انتخاب سيم جوش نيز از اهميت خاصي برخوردار ميباشد.
جدول 9- قابليت جوشکاری MIG
جنس قطعه كار | قابليت جوشکاری | |||||||||||||
ضعيف | متوسط | خوب | عالي | |||||||||||
فولاد نرم | **** | ************** | ******* | |||||||||||
چدن | ******* | ********** | ***** | |||||||||||
فولاد زنگ نزن | ***** | ************** | *** | |||||||||||
آلومينيوم | **** | ********* | *** | |||||||||||
مس | **** | *********** | ****** | |||||||||||
منيزيم | **** | ********* | ** | |||||||||||
تيتانيوم | ***** | *********** | **** | |||||||||||
: محدوده معمول | *: محدوده ممكن * | |||||||||||||
ويژگيهاي سيم جوش
سيم جوش هاي مصرفي در اين فرآيند بر دو نوع ساده و مغزدار بوده و از آلياژهاي مختلف ساخته ميشوند. در جدول زير انواع جنس سيم جوش ها و موارد كاربردشان را مشاهده ميكنيد:
جدول 10- انواع سيم جوش ها و موارد كاربردشان
ويژگيها و كاربرد | جنس سيم جوش |
مناسب براي جوشکاری با گاز محافظ دياكسيدكربن | منگنز و سيليسيم |
مناسب براي جوشکاری با گاز محافظ آرگون و هليم | آلومينيوم |
مناسب براي جوشکاری حساس و دقيق روي فولادهاي كم كربن با گاز دياكسيدكربن | فولاد كمآلياژ |
براي جوشکاریهاي خاص و ايجاد اتصالاتي با تركيبات خاص | مواد سنتزي با مغز پودري |
جوشکاری بر سطوح زنگ زده و فولادهاي نيم كشته | سيم جوش اكسيدكننده |
پارامترهاي عملياتي جوشکاری MIG
سرعت جوشکاری به جنس قطعه كار و جنس سيم جوش بستگي دارد. به عنوان مثال در جدول 11، ويژگيهاي جوشکاری يك قطعه از جنس فولاد كمكربن با الكترودي از جنس فولاد كم كربن را مشاهده مينماييد:
جدول 11- ويژگيهاي جوشکاری يك قطعه از جنس فولاد كمكربن با الكترودي از جنس فولاد كم كربن
نوع اتصال | سرعت پيشروي سيم جوش
(اينچ در دقيقه) |
قطر سيم جوش (اينچ) | سرعت جوشکاری
(اينچ در دقيقه) |
اتصال گوشه به فرم دايرهاي | 500 | 0.045 | 45 |
اتصال لب به لب دايرهاي | 340-380 | 0.030 | 46.6 |
اتصال گوشه ساده | 30-160 | 0.030 | 10 |
اتصال روي هم | 234 | 0.0625 | 60 |
اتصالT | 300 | 0.045 | 16 |
اتصال لب به لب | 400 | 0.045 | 7 |
عوامل موثر در نتيجه فرآيند جوشکاری
عوامل زير بر نتيجه فرآيند جوشکاری موثر ميباشند:
- مقدار جريان الكتريكي
- نوع جريان الكتريكي
- ولتاژ، ميزان پيشگرم و حرارت جوشکاری
- ميزان گاز محافظ در موضع جوشکاری
- تميز بودن سطوح جوشکاری
- سرعت جوشکاری
- جنس سيم جوش و اندازه آن
- قابليت هدايت الكتريكي قطعه كار
- نوع اتصال
- جنس و ويژگي قطعه كار
توان مورد نياز در جوشکاری
ميزان توان مورد نياز در جوشکاری به روش MIG به عوامل متعددي چون سرعت پيشروي الكترود و قطر آن و مواردي اين-چنيني بستگي دارد. در جدول 12، ويژگيهاي جوشکاری يك قطعه از جنس فولاد كمكربن با الكترودي از جنس فولاد كم-كربن را مشاهده ميكنيد:
جدول 12- ويژگيهاي جوشکاری يك قطعه از جنس فولاد كمكربن با الكترودي از جنس فولاد كمكربن
نوع اتصال | سرعت پيشروي سيمجوش
(اينچ در دقيقه) |
قطر سيمجوش (اينچ) | جريان الكتريكي
(آمپر) |
اتصال گوشه به فرم دايرهاي | 500 | 0.045 | 280-300 |
اتصال لب به لب دايرهاي | 340-380 | 0.030 | 170-190 |
اتصال گوشه ساده | 30-160 | 0.030 | 80-85 |
اتصال روي هم | 234 | 0.0625 | 380 |
اتصالT | 300 | 0.045 | 200 |
اتصال لب به لب | 400 | 0.045 | 275 |
محاسبات زمان جوشکاری در روش MIG
زمان جوشکاری به طول درز جوش، تعداد پاسهاي مورد نياز و سرعت جوشکاری بستگي دارد. تعداد پاسها نيز به پهناي درز جوش وابسته است. وقتي پهناي درز جوش زياد باشد، لازم است الكترود را به صورت زيگزاگ حركت داده تا پهناي درز جوش به درستي پر شود.
در شرايطي كه طول محل جوشکاری بر حسب اينچ R، سرعت جوشکاری بر حسب اينچ در دقيقه و تعداد پاس ها N باشد، خواهيم داشت:
time for one pass = L/R
total time = (L/R) * N
لحيم كاري سخت با شعله
در لحيم كاري سخت با شعله، که يك فرآيند جوشکاری است كه در آن با استفاده از يك سيم جوش ميتوان دو قطعه را به هم جوش داد. گرماي مورد نياز فرآيند از يك شعله تامين ميشود. در اثر حرارت، سيم جوش ذوب شده و درز جوش را پر ميكند.
ويژگيهاي فرآيند
- در اين فرآيند، از شعله خروجي يك مشعل براي ذوب كردن سيمجوش استفاده ميشود.
- معمولا قطعات فولادي و چدني به اين روش به هم متصل ميشوند.
- سيم جوش مورد استفاده در اين فرآيند، معمولا از آلياژهاي مس ساخته ميشود.
- در اين فرآيند بايد از فلاكس (پوشش) استفاده نمود.
ماشين و تجهيزات
تجهيزات مورد نياز براي عمليات لحيمكاري سخت با شعله عبارتند از: كپسول حاوي يك گاز سوختني مناسب نظير استيلن، گاز طبيعي يا پروپان، كپسول حاوي اكسيژن (يا هوا)، رگولاتور فشار، مشعل و سيم جوش.
جوشکاری قوس تنگستن تحت پوشش گاز محافظ (TIG)
در عمليات جوشکاری با قوس الكتريكي و الكترود تنگستني با پوشش گاز محافظ Tungsten Inert Gas، قوس الكتريكي بين يك الكترود مصرف نشدني از جنس تنگستن و قطعه كار برقرار ميشود و سيمجوش جداگانه به محل درز جوش هدايت ميگردد. در اين عمليات بايد گاز محافظ خنثي و جريان الكتريكي يكنواختي در موضع جوشکاری برقرار باشند
ويژگيهاي فرآيند
- در اين فرآيند از يك الكترود تنگستني مصرف نشدني براي برقراري قوس استفاده ميشود.
- در اين فرآيند، گازهاي محافظ آرگون و هليم به كار ميروند. استفاده از گازهاي آرگون و هليم به علت خاصيت خنثي بودن اين گازها ميباشد. گازهاي خنثي با عناصر ديگر قابليت واكنش ندارند، پس به منظور حذف گازهاي فعال مانند اكسيژن و نيتروژن از اطراف قوس و حوضچه مذاب، اكسيدها و نيتريدهاي فلزي ايدهآل ميباشند. بدين ترتيب ميتوان از شكل گرفتن تخلخلهاي گازي جلوگيري نمود. تخلخلهاي گازي، اكسيدها و نيتريدهاي فلزي، عيوبي هستند كه باعث كاهش خواص مكانيكي جوش از جمله مقاومت به ضربه و استحكام كششي ميشوند.
- كيفيت جوشکاری با اين فرآيند بسيار خوب ميباشد.
- گلجوش و پراكندگي ذرات جوش در اين فرآيند بهوجود نميآيد.
- براي جوشکاری دستي قطعات نازك مناسب ميباشد.
ماشين و تجهيزات
تجهيزات مورد نياز براي جوشکاری به روشTIG عبارتند از: يك واحد تامين انرژي الكتريكي، آب خنك كننده، گاز محافظ، يك تفنگ جوشکاری دستي، سيم جوش و پدال كنترل پايي. با استفاده از پدال كنترل پايي، اپراتور ميتواند جريان الكتريكي را متناسب با جوشکاری تنظيم نمايد.
فرم الكترود
انتهاي الكترودهاي جوشکاری در روشTIG فرمهاي متنوعي دارد. الكترودهاي نوك تيز و سركروي، پر مصرفتر از بقيه انواع الكترودها ميباشند. براي ساخت الكترودهاي سركروي، ابتدا اين الكترودها را به صورت نوك تيز ساخته، به طوري كه طول قسمت مخروطي آنها سه تا شش برابر قطر الكترود باشد. با گرم شدن اين الكترود، نوك تيز آن ذوب شده و به صورت كروي درميآيد و هماهنگ با جريان الكتريكي اعمالي، فرم كروي ايدهآل به دست ميآيد.
جدول 13- فرم الكترودها و كاربردهايشان
فرم الكترود تنگستني | كاربردها | |
نوك تيز | در جوشکاری با جريان الكتريكي مستقيم با پلاريته مستقيم كاربرد دارد.
– قوس الكتريكي را به محل مورد نظر هدايت ميكند. -براي جوشکاری درزهاي باريك و محل هاي تنگ مناسب است. |
– |
سر كروي | در جوشکاری با جريان الكتريكي مستقيم با پلاريته معكوس به كار ميرود.
– ميتواند بيشترين جريان الكتريكي را هدايت كند. |
– |
انواع تفنگ هاي روش TIG
تفنگ هاي اين روش جوشکاری، براي جوشکاری دستي و در دو نوع خنك شونده با هوا Air cooled و خنك شونده با آب Water Cooled ساخته ميشوند. براي جوشکاری ظريف و سبك تا 150 آمپر، از تفنگهاي خنك شونده با هوا و براي جوشکاریهاي سنگين يا جريان الكتريكي تا 600 آمپر، از تفنگهاي خنك شونده با آب استفاده ميگردد. توان جوشكاری هر تفنگ روي آن درج ميشود.
جنس الكترود و اندازه آن
اندازه الكترود بايد با دقت و بر اساس جنس قطعه كار، جريان الكتريكي و ضخامت قطعه كار تعيين گردد. تنگستن خالص از ارزانترين الكترودها ميباشد. در بعضي از الكترودها، عناصري مثل زيركونيوم و توريم اضافه ميگردد. اين عناصر سبب بهبود كارايي الكترود ميشود. جدول زير انواع الكترودها را بر حسب كاربردشان نشان ميدهد:
جدول 14- انواع الكترودها بر حسب كاربردشان
ويژگي و كاربرد | جنس الكترود | |
مناسب براي جوشکاری با جريان الكتريكي پايين | – | تنگستن خالص |
براي جوشکاری عمومي و با حساسيت كمتر | – | |
برقراري قوس الكتريكي با اين الكترود بدون پاشش و جرقه است | – | تنگستن- توريم |
پايداري قوس با اين الكترود بهتر است | – | |
فرم نقطه انتهايي جوش با اين الكترود خوب و يكنواخت است | – | |
جلوگيري از آلوده شدن محل جوش | – | تنگستن- زيركونيوم |
فرم نقطه انتهاي جوش با اين الكترود، خوب و يكنواخت است | – | |
براي جوشکاری با جريان الكتريكي متناوب پايين | – |
گاز محافظ
آرگون از پرمصرف ترين گازهاي محافظ در جوشکاری به اين روش ميباشد. ويژگي و كاربرد سه نوع گاز محافظ در جدول زير آورده شده است:
جدول 15- ويژگي و كاربرد سه نوع گاز محافظ
ويژگي و كاربرد | نوع گاز محافظ | |
هزينه پايين و مناسب جهت جوشکاری انواع فلزات | – | آرگون |
مناسب براي جريانهاي الكتريكي پايين | – | |
برقراري راحت قوس الكتريكي، يكنواخت و پايداري آن | – | |
مورد استفاده در جوشکاری فولاد نرم، آلومينيوم و تيتانيوم | – | |
امكان برقراري جريان گاز تا 3- 1.5 برابر آرگون | – | هليم |
جوشکاری سريعتر فولاد نرم و تيتانيوم | – | |
ايجاد ناحيه متاثر از جوش باريك تر و نفوذ بيشتر جوش | – | |
امكان برقراري قوس متراكم و گرمتر | – | |
امكان افزايش سرعت جوشکاری تا 40- 30 درصد | – | |
مناسب جهت جوشکاری فولاد زنگنزن و مس | – | |
براي ايجاد قوس الكتريكي گرمتر در جوشکاری آلومينيوم | – | مخلوط آرگون- هليم |
مورد استفاده در عمليات جوشکاری اتوماتيك | – | |
مناسب براي جوشکاری آلومينيوم | – |
قابليتهاي فرآيند
اين جوشکاری، قابليت اتصال لب به لب، روي هم، گوشه و لبه دار را فراهم ميكند. كيفيت جوش حاصل، تا حد زيادي به آماده سازي لبه هاي قطعه كار، بستگي دارد.
كيفيت جوشکاری TIG
با در نظر گرفتن مواردي چون: تميز نگهداشتن موضع جوشکاری و ديگر تجهيزات، اطمينان از انتخاب صحيح تجهيزات جوشکاری و پارامترهاي فرآيند، استفاده از تكنيك صحيح جوشکاری و جنس سيم جوش و الكترود، ميتوان از بروز عيوب جوشکاری نظير ترك، حفره، گرده جوش كثيف و برجسته و عدم ذوب كامل، جلوگيري كرد.
جدول 16- انواع عيوب و علل ممكن از جوشکاری TIG
اثرات نامطلوب | علل ممكن | نوع عيب | ||
استحكام ناكافي محل جوش | – | تنشهاي مكانيكي تنشهاي حرارتي
وجود مشكلات متالورژيكي |
–
– – |
ترك |
استحكام ناكافي محل جوش | – | ناكافي بودن گاز محافظ
به تله افتادن گاز در محل جوش جريان الكتريكي بالا |
–
– – |
حفره |
ظاهر بد محل جوش جوش شكننده
ايجاد حفره يا ترك در جوش |
–
– – |
نفوذ آب يا هوا در محل عبور گاز محافظ
جريان الكتريكي بالا |
–
– |
گرده جوش كثيف و برجسته |
كاهش استحكام استاتيكي ايجاد نقاط تمركز تنش | –
– |
سطوح كثيف قطعه كار سرعت بالاي جوشکاری جريان الكتريكي پايين | –
– – |
عدم ذوب كامل |
اثرات جوشکاری TIG بر خواص ماده
بعضي از اثرات اين نوع جوشکاری بر خواص مواد، در جدول زير ارايه شده است:
جدول 17- اثرات جوشکاری TIG بر خواص ماده
اثرات جوشکاری بر خواص ماده | خواص ماده | |
ممكن است باعث سخت شدن ماده شود. | – | مكانيكي |
ممكن است باعث كاهش استحكام خستگي قطعه شود. | – | |
قطعه كار احتمالا دچار پيچيدگي ميشود. | – | |
ممكن است باعث نرمشدن ماده شود. | – | |
در قطعه كار انقباض بهوجود ميآيد. | – | |
كيفيت ظاهري بد | – | فيزيكي |
احتمال ايجاد حفره يا ترك | – | |
احتمال كاهش مقاومت در برابر خوردگي | – | شيميايي |
جنس قطعه كار
معمولا فلزات غيرآهني نظير آلومينيوم، منيزيم، تيتانيم و فلزات ديرگداز، با اين روش، جوشکاری ميشوند. البته ميتوان فولاد زنگ نزن، چدن و فولاد نرم را نيز با اين روش، جوشکاری نمود.
جدول 18- قابليت جوشکاری TIG
جنس قطعه كار | قابليت جوشکاری | ||||||||||||
ضعيف | متوسط | خوب | عالي | ||||||||||
فولاد نرم | ********* | ******* | ******* | ||||||||||
چدن | ********* | ******** | ******* | ||||||||||
فولاد زنگ نزن | ******* | ***** | ******** | ||||||||||
آلومينيوم | **** | ******* | *** | ||||||||||
مس | **** | ********* | *** | ||||||||||
تيتانيوم | ***** | *********** | **** | ||||||||||
: محدوده معمول | *: محدوده ممكن * | ||||||||||||
عوامل موثر در نتيجه فرآيند جوشکاری
در صورتي كه جوشكار به اندازه كافي ماهر باشد، ميتواند يك گرده جوش صاف و يكنواخت به وجود آورد. اين نوع جوشکاری، عموما براي اتصال قطعات نازك به كار ميرود. ويژگيهايي كه بر قابليت اين نوع جوشکاری موثر ميباشند عبارتند از:
- فرم قطعه كار
- ضخامت قطعه كار
- نوع آلياژ
- مقاومت الكتريكي
- هدايت گرمايي
- انبساط در اثر گرما
- سختي و استحكام
- ويژگي اكسيده شدن ماده
عوامل موثر بر كيفيت جوشکاری به روش TIG عبارتند از:
- جريان و ولتاژ الكتريكي
- نوع جريان الكتريكي
- ميزان گاز محافظ در موضع جوشکاری
- تميز بودن سطوح قطعه كار
- سرعت جوشکاری و رسوب سيم جوش در درز جوشکاری
- جنس الكترود و فرم سر آن
- هدايت الكتريكي قطعه كار
- طراحي اتصال
- جنس و ويژگيهاي قطعه كار
توان مورد نياز
در جدول زير، محدوده جريان الكتريكي مجاز براي الكترودهاي با قطرهاي متفاوت ارايه شده است. قطر الكترود بايد با دقت انتخاب شود. قطر الكترود بستگي به جنس قطعه كار، جريان الكتريكي و ضخامت قطعه كار دارد.
جدول 19- محدوده جريان الكتريكي مجاز براي الكترودهاي با قطرهاي متفاوت
قطر الكترود | جريان مستقيم | جريان متناوب | ||
پلاريته مستقيم | پلاريته معكوس | الكترود تنگستن | الكترود تنگستني با عناصر زيركونيوم و توريم | |
0.010 | حداكثر 15 | NR | حداكثر 15 | حداكثر 15 |
0.020 | 5-20 | NR | 5-15 | 5-20 |
1/16 | 70-150 | 10-20 | 50-100 | 70-150 |
3/32 | 150-250 | 15-30 | 100-160 | 140-235 |
1/8 | 250-400 | 25-40 | 150-210 | 225-325 |
3/16 | 500-750 | 55-80 | 250-350 | 400-500 |
1/4 | 750-1000 | 80-125 | 325-450 | 500-630 |
محاسبات زمان جوشکاری در روش TIG
زمان جوشکاری به طول درز جوش، تعداد پاسهاي مورد نياز و سرعت جوشکاری بستگي دارد. تعداد پاسها نيز به پهناي درز جوش وابسته است. وقتي پهناي درز جوش زياد باشد، لازم است الكترود را به صورت زيگزاگ حركت داده تا پهناي درز جوش به درستي پر شود.
در شرايطي كه طول محل جوشکاری بر حسب اينچ R، سرعت جوشکاری بر حسب اينچ در دقيقه و تعداد پاس ها N باشد، خواهيم داشت:
time for one pass = L/R
total time = (L/R) * N
جوشکاری با پرتوي ليزر
در جوشکاری با پرتوي ليزري، حرارت مورد نياز براي ذوب كردن فلز، از تابش يك پرتوي متمركز و باريك از نور تكرنگ حاصل ميشود. معمولا در اين روش جوشکاری از سيمجوش استفاده نميشود.
ويژگيهاي فرآيند
- براي جوشکاری قطعات نازك و ظريف مناسب است.
- معمولا براي جوشکاری نقاطي از قطعه كار كه در دسترس نيست، به كار ميرود.
- دقت جوشکاری در اين روش، بسيار بالا ميباشد.
- در اين روش ميتوان فلزات ناهمجنس را به هم متصل نمود.
- در جوشکاری با ليزر از سيمجوش استفاده نميشود.
- تقريبا هيچ آسيب حرارتي به قطعه كار وارد نميشود.
- جوشکاری با ليزر را ميتوان به راحتي اتوماتيك نمود.
انواع پرتوهاي ليزر
پرتوي ليزر گازي دياكسيدكربن يا ليزر حالت جامد Nd:YAG (neodymium-doped yttrium aluminium garnet)، با عبور از عدسي ها و آيينه ها در نقطه مورد نظر متمركز ميشود. موج پرتوي ليزر دياكسيدكربن تقريبا 10.6 ميكرومتر و طول موج پرتوي ليزر Nd:YAG، در حدود 1.06 ميكرومتر ميباشد. قطر نقطه تمركز ليزر، تقريبا 10 برابر طول موج آن ميباشد.
عيوب حاصل از جوشکاری ليزر
در جدول زير، عيوب رايج مشاهده شده در عمليات جوشکاری با پرتوي ليزر و علل احتمالي اين عيوب را مشاهده ميكنيد:
جدول 20- عيوب رايج در عمليات جوشکاری با پرتوي ليزر
اثرات نامطلوب | علل احتمالي | نوع عيب |
كاهش استحكام | سرعت زياد جوشکاری ، تمركز ناكافي
پرتوي ليزر، توان ناكافي پرتوي ليزر، پهناي زياد درز جوش |
حفره |
كاهش استحكام، اعوجاج در قطعه كار | سرعت كم جوشکاری، تمركز ناكافي پرتوي ليزر، توان بيش از حد پرتوي
ليزر |
تنشهاي داخلي |
اثرات جوشکاری ليزر بر خواص ماده
جوشکاری با ليزر، اثرات اندكي بر خواص مواد مختلف دارد.
جدول 21- اثرات جوشکاری ليزر بر خواص ماده
اثرات جوشكاری ليزر بر خواص ماده | خواص ماده |
احتمال سخت شدن يا نرم شدن قطعه كار | مكانيكي |
اثري ندارد | فيزيكي |
اثري ندارد | شيميايي |
پارامترهاي مهم فرآيند و عوامل موثر در نتيجه آن
عوامل زير نقش بسيار مهمي را در اجرا و نتيجه فرآيند جوشکاری با پرتوي ليزر دارند:
- جنس قطعه كار (هدايت گرمايي و قابليت انعكاس نور)
- طراحي اتصال جوشکاری
- نوع و توان پرتوي ليزر
- موقعيت محل تمركز پرتوي ليزر روي قطعه
- دقت تمركز پرتو
- سرعت جوشکاری
- فركانس پالس هاي پرتوي ليزر
- زمان هر پالس
- نوع و ميزان گاز محافظ
- طرح نازل خروج گاز
عوامل موثر در قابليت جوشکاری يك قطعه كار با پرتوي ليزر، عبارتند از:
- وضعيت سطح قطعه كار
- جنس قطعه كار
- ضخامت قطعه كار
- نحوه تمركز پرتوي ليزر
- توان اعمالي پرتوي ليزر
- نقطه ذوب ماده
- طرح اتصال جوشکاری
لحيم كاري غوطه وري
اين فرآيند نيز يكي از فرآيندهاي اتصال قطعات و جوشکاری است كه در آن قطعات با غوطه ور شدن در يك حمام از ماده لحيم كاري مذاب، به هم لحيم ميشوند. با توجه به پايين بودن دماي لحيم كاري، قطعه كار و ماده لحيم كاري در واقع فقط به يكديگر ميچسبند. براي آمادهسازي سطح قطعه كار بايد از يك ماده تميزكننده استفاده نمود. لحيم كاري غوطه وري، يك فرآيند اتوماتيك به حساب آمده كه در صنعت الكترونيك، كاربرد فراواني دارد.
ويژگيهاي فرآيند
- ماده لحيم كاري مذاب در يك ظرف ريخته شده و قطعه كار در آن غوطه ور ميشود.
- در اين فرآيند بايد از فلاكس استفاده نمود.
- دماي اجراي اين فرآيند نسبتا پايين است و هيچيك از قطعات ذوب نميشوند.
- زمان غوطه وري معمولا بين 2 تا 12 ثانيه است.
- اين فرآيند به خوبي قابل اتوماسيون است.
- اين فرآيند در صنايع الكترونيك كاربرد فراواني دارد.
ماده لحيم كاري
اين ماده معمولا آلياژي حاوي 50 درصد قلع، 49.5 درصد سرب و 0.5 درصد آنتيموان است. پايين بودن دماي ذوب ماده لحيم كاري به دليل وجود سرب در اين ماده است. وجود قلع نيز سبب پخش شدن خوب و سريع ماده روي سطح كار ميشود.
جوشکاری با قوس پلاسما
در جوشکاری با قوس پلاسما يك قوس الكتريكي داخلي، بين الكترود مصرف نشدني از جنس تنگستن و بدنه شعله جوشکاری برقرار ميشود. با عبور گاز خنثي از ميان قوس الكتريكي، گاز فوقالعاده داغ شده و به پلاسما تبديل ميگردد. از اين جريان پلاسما كه به سمت قطعه كار جاري ميشود، براي ذوب كردن سيم جوش استفاده ميشود.
شکل42- جوشکاری با قوس پلاسما
ويژگيهاي فرآيند
- در اين عمليات از يك الكترود مصرف نشدني از جنس تنگستن استفاده ميشود.
- براي ايجاد پلاسما و همچنين به عنوان گاز محافظ، از يك گاز خنثي نظير آرگون، هليم يا نيتروژن استفاده ميشود.
- حرارت ايجادشده در قوس پلاسما، ممكن است به 30000 درجه فارنهايت برسد.
ماشين و تجهيزات
تجهيزات مورد نياز براي جوشکاری با قوس پلاسما عبارتند از: يك ماشين جوشکاری كه قابليت تنظيم جريان الكتريكي را داشته باشد، كپسول حاوي گاز خنثي، سيستم خنككننده آبي، سيستم كنترل جريان الكتريكي و گاز، يك سوييچ قطع و وصل كه ترجيحا به صورت يك پدال پايي عمل كند، يك مشعل دستي يا اتوماتيك و منبع قدرت الكتريكي.
اكترود و سيم جوش
الكترود مورد استفاده در فرآيند جوشکاری با قوس پلاسما، يك الكترود تنگستني مصرف نشدني است و بنابراين لازم است از سيم جوش براي جوشکاری قطعه كار استفاده شود.
فرم سر مشعل
در جدول زير دو نوع مشعل با كاربردهايشان را مشاهده ميكنيد:
جدول 22- انواع مشعل و كاربردهايشان
نوع سرمشعل | فرم | كاربرد |
يك سوراخه | جوشكاری ساده، عمومي | |
چند سوراخه | براي ايجاد قوسهاي بلند و افزايش سرعت جوشكاری بزرگ تا 50 درصد |
الكترود و جريان الكتريكي
در جدول زير، جريان الكتريكي مناسب براي قطرهاي مختلف الكترود ارايه شده است:
جدول 23- جريان الكتريكي مناسب براي قطرهاي مختلف الكترود
قطر الكترود تنگستني (اينچ) | جريان الكتريكي (آمپر) |
0.010 | حداكثر 15 |
0.020 | 5-20 |
0.040 | 15-80 |
1/16 | 70-150 |
3/32 | 150-250 |
1/8 | 250-400 |
5/32 | 400-500 |
در جدول 24، انواع گازهاي محافظ اين روش جوشکاری و موارد كاربردشان را مشاهده مينماييد:
جدول 24- انواع گازهاي محافظ و موارد كاربردشان
كاربردها | نوع گاز محافظ |
جوشكاری فولاد كربني و كمآلياژ، جوشكاری مس و روي | آرگون |
جوشكاری فولاد زنگنزن، جوشكاری نفوذي سريع، جوشكاری پاسهاي اوليه درز جوشهاي بزرگ | مخلوط آرگون و اكسيژن |
جوشكاری ذوبي معمولي، جوشكاری مس و فولاد زنگنزن، جوشكاری نفوذي سريع | هليم |
كيفيت جوشکاری و عيوب رايج آن
در جدول زير، عيوب رايج در جوشکاری پلاسما و علل احتمالي آنها ارايه شده است:
جدول 25- عيوب رايج و علل احتمالي آنها
اثرات نامطلوب | علل احتمالي | عيب | ||
كاهش استحكام جوش | – | تنشهاي مكانيكي تنشهاي حرارتي
ناخالصي در آلياژ قطعه كار يا سيمجوش |
–
– – |
ترك |
كاهش استحكام جوش | – | گاز محافظ ناكافي حبس شدن گاز در فلز مذاب | –
– |
حفره (تخلخل) |
ظاهر بد | – | جريان الكتريكي بالا | – | گرده جوش كثيف و خشن |
كاهش استحكام استاتيكي | – | سطوح كثيف قطعه | – | ذوب نشدن كامل فلز |
احتمال ايجاد تمركز تنش | – | سرعت زياد جوشكاریی | – |
اثرات جوشکاری پلاسما بر خواص ماده
جدول 26- اثرات جوشکاری پلاسما بر خواص ماده
اثرات جوشكاری پلاسما بر خواص ماده | خواص ماده | |
احتمال سخت شدن قطعه كار | – | مكانيكي |
تردید كاهش استحكام خستگي | – | |
شایدی ايجاد انقباض | – | |
شایمندی نرم شدن قطعه كار | – | |
گمانه ايجاد اعوجاج و پيچيدگي قطعهكار | – | |
ظاهر بد قطعه كار | – | فيزيكي |
احتمال ايجاد حفره | – | |
احتمال كاهش مقاومت خوردگي | – | شيميايي |
عوامل موثر در نتيجه فرآيند
عواملي كه در نتيجه جوشکاری پلاسما موثر ميباشند عبارتند از:
- حرارت شعله پلاسما
- ميزان خروج گاز محافظ
- تميز بودن موضع جوشکاری
- سرعت جوشکاری
- طرح اتصال جوش
- جنس و ويژگيهاي قطعه كار
توان مورد نياز
توان مورد نياز در اين فرآيند، به جنس قطعه كار و ضخامت آن بستگي دارد.
جدول 27- توان مورد نياز در فرآيند جوشكاری پلاسما
جنس قطعه كار |
توان مورد نياز (آمپر) | |||
ضخامت قطعه كار (اينچ) | ||||
0.093 | 0.125 | 0.187 | 0.250 | |
فولاد كمآلياژ | 145 | 185 | 215 | 275 |
فولاد زنگنزن | 115 | 145 | 165 | 240 |
آلياژهاي تيتانيوم | 165 | 185 | 175 | 200 |
مس و برنج | 180 | 300 | 460 | 670 |
نقطه جوش برجسته
عمليات نقطه جوش برجسته يك فرآيند اتصال فلزات است كه در آن يك قطعه كار با چند نقطه برجسته روي يك قطعه كار ديگر قرار ميگيرد و با عبور جريان الكتريكي از قطعات، اين نقاط تماس گرم ميشوند. دو الكترود مصرف نشدني قطعات را روي هم ميفشارند و ضمن هدايت جريان الكتريكي، با اعمال فشار باعث جوش خوردن دو قطعه به يكديگر خواهد شد.
ويژگيهاي فرآيند
- در اين فرآيند از سيم جوش استفاده نميشود.
- سطح يكي از قطعات براي انجام اين عمليات بايد چند نقطه برجسته داشته باشد.
- با يك حركت ماشين، ميتوان چند نقطه جوش روي قطعه كار ايجاد نمود.
- در اين عمليات از دو الكترود مسي مصرف نشدني استفاده ميشود.
- اين عمليات معمولا براي اتصال قطعات با ضخامت كم به كار ميرود.
- اين عمليات را به راحتي ميتوان مكانيزه نمود.
ماشين و تجهيزات
در اين فرآيند معمولا از يك ماشين پرس مخصوص استفاده ميشود. روي اين پرس، الكترودهايي براي انتقال جريان الكتريكي و تابلوي كنترل جريان تعبيه شده است. نيروي پرس نيز ميتواند به صورت هيدروليكي، نيوماتيكي، فنري يا الكترومغناطيسي تامين گردد.
الكترودها
در اين فرآيند معمولا از الكترودهاي سرتخت استفاده ميشود. اين الكترودها ميتوانند فشار كافي به قطعه كار وارد كرده و جريان الكتريكي لازم را به موضع جوشكاری هدايت نمايند. اين الكترودها بايد داراي خواصي مانند هدايت الكتريكي خوب، استحكام كافي، سختي و مقاومت در برابر حرارت باشند.
قابليت هاي فرآيند
ضخامت قطعه كار براي انجام اين فرآيند معمولا بين 005. تا 0.5 اينچ انتخاب ميشود.
كيفيت و عيوب نقطه جوش برجسته
معمولا عيوب نقطهجوش هنگامي بهوجود ميآيد كه جريان و فشار الكترود بهدرستي تنظيم نشده باشند. اگر كيفيت نقطه جوش بد باشد، علاوه بر ظاهر نامناسب، باعث كاهش استحكام خستگي و افزايش احتمال خوردگي در قطعه كار ميشود.
جدول 28- كيفيت و عيوب نقطه جوش برجسته
اثرات نامطلوب | علل احتمالي | عيب | ||
كاهش استحكام جوش ظاهر | –
– |
نيروي زياد الكترود حرارت بيش از حد | –
– |
فرورفتگي سطح |
ايجاد نقطه جوش كوچك سوراخ شدن محل نقطه جوش | –
– |
نيروي كم الكترود جريان الكتريكي زياد | –
– |
ذوب شدن محل جوش |
كاهش استحكام جوش | – | ساييدگي سطح الكترود نامنظم بودن فرم برجستگي | –
– |
فرم نقطه جوش نامنظم باشد |
كاهش استحكام خستگي افزايش خوردگي | –
– |
حرارت بيش از حد
جداشدن پيش از موعد الكترود از قطعه كار سطح كثيف قطعه كار |
–
– – |
ايجاد ترك و حفره در محل نقطه جوش |
اثرات نقطه جوش برجسته بر خواص مواد
یکی از اثرات اين فرآيند بر خواص مكانيكي عبارتند از: سخت شدن، نرم شدن، پيچيدگي و كاهش استحكام خستگي. اثرات نقطه جوش بر خواص فيزيكي ماده عبارتند از: ظاهر بد، ترك هاي داخلي، حفره و ترك هاي سطحي. تنها اثر اين فرآيند بر خواص شيميايي ماده عبارتند از كاهش مقاومت خوردگي.
جنس الكترود
در جدول 29، انواع گوناگوني از الكترودهاي بهكار رفته در اين روش، به همراه كاربردشان را مشاهده ميكنيد:
جدول 29- انواع الكترودها به همراه كاربردشان
كاربردها | جنس الكترود | |
نقطه جوش فولاد كمكربن گالوانيزه و قلعاندود | – | آلياژ مس (كلاس 1) |
نقطه جوش كرم، روي و آلومينيوم | – | |
نقطه جوش فولاد كمكربن نوردشده گرم و سرد | – | آلياژ مس (كلاس 2) |
نقطه جوش فولاد زنگنزن | – | |
نقطه جوش آلياژهاي نيكل | – | |
جوشكاری برنز سيليسيمدار و آلياژ نقره- نيكل | – | |
نقطه جوش با فشار زياد و جوشدادن مواد با مقاومت الكتريكي بالا | – | آلياژ مس (كلاس 3) |
جوشدادن فولاد كمكربن ضخيم | – | |
نقطه جوش فولاد زنگنزن | – | |
نقطه جوش مونل و اينكونل | – | |
اعمال حرارت زياد در نقطه جوش اعمال زمان طولاني | –
– |
فلزات ديرگداز، كلاس
10 الي 14 |
اعمال فشار بالا به هنگام جوشكاری | – | |
عدم امكان خنككاري الكترود | – |
عوامل موثر در نتيجه فرآيند
عوامل موثر در نتيجه عمليات نقطه جوش برجسته عبارتند از: فرم برجستگي، ميزان هدايت الكتريكي و حرارتي الكترود، جريان الكتريكي، فرم و جنس الكترود، نيروي اعمالي الكترود، زمان جوشكاری، فواصل بين نقطه جوشها، جنس قطعه كار و تميز بودن سطح قطعات.
جوشکاری با قوس الكتريكي و الكترود پوشش دار
در عمليات جوشکاری با قوس الكتريكي و الكترود پوشش دار كه به اختصار SMAW ناميده ميشود، قوس الكتريكي بين يك الكترود فلزي مصرف شدني پوششدار و قطعه كار برقرار ميشود. در اثر حرارت حاصل از قوس الكتريكي، پوشش جامد الكترود به صورت گاز درآمده و يك حفاظ گازي در پيرامون محل جوشکاری ايجاد ميكند. قسمتي از اين پوشش نيز ذوب شده و به صورت گل جوش روي گرده جوش مينشيند.
ويژگيهاي فرآيند
- در اين روش از يك الكترود ميلهاي مصرف شدني استفاده ميشود.
- پوشش روي الكترود، در اثر حرارت ذوب شده و روي گرده جوش رسوب ميكند.
- مقداري از پوشش الكترود نيز در اثر حرارت به صورت گاز درآمده و فضاي جوشکاری را حفاظت ميكند.
- جريان ثابتي به هنگام جوشکاری مصرف ميشود.
- كيفيت ظاهري جوش و استحكام آن به مهارت اپراتور در ثابت نگهداشتن طول قوس الكتريكي و سرعت جوشکاری بستگي دارد.
فرم اتصال جوش
در شكل زير انواع جوشها را كه از چپ به راست، به ترتيب به صورت جوش قابل قبول، جوش با آمپر پايين، جوش با آمپر بالا، جوش با طول قوس كوتاه، جوش با طول قوس بلند، جوش با سرعت جوشکاری كم و جوش با سرعت جوشکاری زياد ميباشند را مشاهده ميكنيد:
ماشين و تجهيزات
تجهيزات مورد نياز در اين روش عبارتند از: ماشين جوشکاری قوس الكتريكي كه يك جريان الكتريكي ثابت توليد كرده و به الكترود ارسال ميكند، كابل اتصال به بدنه كه قطعهكار را به ماشين جوشکاری متصل ميكند و همچنين ابزار نگهداري الكترود. ميزان جريان الكتريكي به قطر الكترود وابسته است. معمولا براي هر 100.0 اينچ قطر الكترود بايد 1 آمپر جريان صرف نمود. البته نوع پوشش و جنس الكترود نيز در ميزان جريان الكتريكي موثر است.
الكترود
قطر الكترودهاي مورد مصرف در اين فرآيند، معمولا بين 16/5 تا 16/1 اينچ و طول آنها نيز 9، 14 و 18 اينچي ميباشد. جنس الكترود بايد متناسب با جنس قطعه كار انتخاب شود. الكترودهاي پوششدار معمولا از فولاد نرم، فولاد زنگ نزن، نيكل و برنز ساخته ميشوند. كدگذاري الكترودها، در جدول زير با موارد كاربردشان نشان داده شده است. در اين كدگذاريها، حرف انگليسي نشانه الكترود، دو عدد اول از سمت چپ نشاندهنده استحكام كششي بر حسب كيلوپاسكال يا پوند بر اينچ مربع، عدد بعد نشاندهنده وضعيت جوشکاری و عدد آخر نشاندهنده نوع جريان الكتريكي ميباشد.
جدول 30- كدگذاري الكترود ها
كد الكترود | كاربردها |
E6010 E6011 | عمق نفوذ زياد، قوس الكتريكي قوي و انتقال قوس و مواد مذاب بهصورت پاششي |
E6012 E6013 | عمق نفوذ متوسط، انتقال مواد مذاب بهصورت قطرهاي، جوشكاری ورقهاي فلزي |
E6020 | انتقال قوس و مواد مذاب بهصورت پاششي، عمق نفوذ متوسط، ايجاد گل جوش متخلخل و لانه زنبوري |
در جدول زير، انواع مواد مصرفي در پوشش الكترودهاي فولادي نرم به همراه كاربرد آنها ارايه شده است.
جدول 31- انواع مواد مصرفي در پوشش الكترودهاي فولادي نرم به همراه كاربرد آنها
كاربردها | مواد بهكاررفته در پوشش الكترود فولادي نرم | |
ايجاد گاز محافظ | – | كلسيم كربنات |
تميزكننده سطح | – | |
سازنده گلجوش | – | تيتانيم دياكسيد |
تثبيت كننده قوس الكتريكي | – | |
تثبيت كننده قوس الكتريكي | – | ميكا |
ايجاد كننده تماس جوشكاری | – | پودر آهن |
افزايش سرعت رسوب مذاب | – | |
آلياژساز | – | فرومنگنز |
اكسيژنزدا | – |
قابليت هاي فرآيند
با اين روش ميتوان انواع اتصالات رايج نظير اتصال لب به لب، اتصال روي هم و اتصال لبه دار را جوشکاری نمود. تنها محدوديت اين روش جوشکاری ، دستي بودن اين روش ميباشد. ضخامت قطعه كار ممكن است از 0.125 تا 12 اينچ باشد.
كيفيت و عيوب جوشکاری با قوس الكتريكي و الكترود پوشش دار
در جدول زير، 5 عيب رايج در اين روش جوشکاری به همراه علل احتمالي و اثرات نامطلوب آنها ارايه شده است:
جدول 32- عيوب رايج در جوشکاری با قوس الكتريكي و الكترود پوشش دار به همراه علل احتمالي و اثرات نامطلوب آنها
اثرات نامطلوب | علل احتمالي | عيب | ||
جوش تركدار قابل قبول نبوده و بايد تكرار شود | – | تنشهاي مكانيكي تنشهاي حرارتي
ورود ناخالصي در آلياژ قطعهكار يا الكترود |
–
– – |
ترك |
كاهش استحكام جوش | – | سطوح كثيف قطعهكار حبس شدن گاز در مذاب | –
– |
حفرههاي زيرسطح |
ظاهر بد | – | جريان الكتريكي زياد | – | گرده جوش خشن و ناصاف |
كاهش استحكام جوش
ايجاد نقاط تمركز تنش |
–
– |
سطوح كثيف قطعه كار سرعت جوشكاری زياد | –
– |
عدم ذوب كامل |
كاهش استحكام جوش | – | حبس شدن گلجوش يا ديگر آلودگيها در مذاب | – | آخال26 |
اثرات جوشکاری با قوس الكتريكي و الكترود پوششدار بر خواص ماده
جدول 33- اثرات جوشکاری با قوس الكتريكي و الكترود پوشش دار بر خواص ماده
اثرات فرآيند بر خواص ماده | خواص ماده | |
احتمال سخت شدن ماده | – | مكانيكي |
گمانه كاهش استحكام خستگي | – | |
شایدی ايجاد انقباض در قطعه كار | – | |
گمانه نرم شدن ماده | – | |
ظن پيچيدگي و اعوجاج در قطعه كار | – | |
ظاهر بد | – | فيزيكي |
حدس ايجاد ترك يا تخلخل در محل جوش | – | |
احتمال كاهش مقاومت خوردگي در ناحيه جوشكاری شده | – | شيميايي |
جنس قطعه كار
اين روش جوشکاری تقريبا به فلزات آهني اختصاص دارد. قابليت جوشکاری فولاد نرم، فولاد زنگ نزن و چدن به روش جوشکاری با قوس الكتريكي و الكترود پوشش دار در حد متوسط تا عالي ميباشد.
عوامل موثر در نتيجه فرآيند
عوامل مهم در كيفيت جوشکاری با قوس الكتريكي و الكترود پوشش دار عبارتند از:
- جريان الكتريكي و ولتاژ جوشکاری
- نوع جريان الكتريكي
- عملكرد پوشش محافظ در پيرامون قوس و روي گرده جوش
- تميز بودن منطقه جوشکاری
- سرعت جوشکاری و سرعت رسوب مذاب
- هدايت الكتريكي قطعه كار
- طرح اتصال دو قطعه
- جنس و خواص قطعه كار
توان مورد نياز
در جدول زير، توان مورد نياز به صورت جريان الكتريكي مصرفي، براي جوشکاری فولاد كم كربن ارايه شده است. جريان مصرفي به سرعت رسوب مذاب، قطر الكترود و نوع الكترود بستگي دارد.
جدول 34- جوشکاری فولاد كم كربن با الكترود فولادي كم كربن
كد الكترود | سرعت رسوب مذاب (اونس/ساعت) | قطر الكترود (اينچ) | جريان مصرفي (آمپر) |
E6011 | 88 | 3/16 | 200 |
E6012 | 66 | 3/16 | 225 |
E7014 | 87 | 3/16 | 260 |
E7018 | 83 | 3/16 | 240 |
E7024 | 134 | 3/16 | 270 |
محاسبات زمان
زمان جوشکاری به طول درز جوش، تعداد پاسهاي مورد نياز و سرعت جوشکاری بستگي دارد. تعداد پاسها نيز به پهناي درز جوش وابسته است. وقتي پهناي درز جوش زياد باشد، لازم است الكترود را به صورت زيگزاگ حركت داده تا پهناي درز جوش به درستي پر شود. در شرايطي كه طول محل جوشکاری بر حسب اينچ R، سرعت جوشکاری بر حسب اينچ در دقيقه و تعداد پاس ها N باشد، خواهيم داشت:
time for one pass = L/R
total time = (L/R) * N
جوشکاری نقطه جوش
نقطه جوش يك فرآيند اتصال قطعات است كه در آن نقاط تماس دو قطعه فلزي بر اثر عبور جريان الكتريكي از آنها، به واسطه مقاومت الكتريكي آنها گرم شده و به هم متصل ميشوند. دو قطعه به هنگام گرم شدن، تحت فشار دو الكترود نيز قرار ميگيرند.
ويژگيهاي فرآيند جوشکاری نقطه جوش
- در عمليات نقطه جوش از فلاكس و ماده پركننده استفاده نميشود.
- سرعت انجام اين عمليات بالا ميباشد.
- به راحتي قابل اتوماسيون است.
- اجراي اين عمليات احتياج به اپراتور ماهر ندارد.
- الكترودهاي مورد استفاده در اين روش، معمولا از جنس مس هستند و مصرفشدني نميباشند.
جنس و مشخصات الكترود
الكترودهاي نقطه جوش كه هدايت كننده جريان الكتريسيته و قطعه اعمال فشار به قطعات هستند، از آلياژهاي مس با مقاومت الكتريكي پايين ساخته ميشوند و معمولا توخالي بوده تا بتوان آنها را با آب خنك كاري نمود. اندازه نوك الكترود به طور مستقيم بر اندازه نقطه جوش و استحكام برشي محل جوشكاری شده، تاثيرگذار ميباشد. براي كاربردهاي خاص ممكن است از تركيبات فلزي ديرگداز استفاده شود. آلياژ مس كلاس 2، پرمصرفترين ماده در ساخت الكترودهاي نقطه جوش ميباشد.
جدول 35- انواع الكترودها به همراه كاربردشان
كاربردها | جنس الكترود | |
نقطه جوش فولاد كم كربن گالوانيزه و قلع اندود | – | آلياژ مس (كلاس 1) |
نقطه جوش كرم، روي و آلومينيوم | – | |
نقطه جوش فولاد كم كربن نوردشده گرم و سرد | – | آلياژ مس (كلاس 2) |
نقطه جوش فولاد زنگ نزن | – | |
نقطه جوش آلياژهاي نيكل | – | |
جوشكاری برنز سيليسيم دار و آلياژ نقره- نيكل | – | |
نقطه جوش با فشار بالا و جوش دادن مواد با مقاومت بالا | – | آلياژ مس (كلاس 3) |
جوشدادن فولاد كم كربن ضخيم | – | |
نقطه جوش فولاد زنگ نزن | – | |
نقطه جوش مونل و اينكونل | – | |
اعمال حرارت زياد در نقطه جوش اعمال زمان طولاني | –
– |
فلزات ديرگداز، كلاس
10 الي 14 |
اعمال فشار بالا به هنگام جوشكاری | – | |
عدم امكان خنك كاري الكترود | – |
قابليتهاي فرآيند جوشکاری نقطه جوش
قطعات بايد به گونهاي بين دو فك قرار بگيرند كه مانع حركت آنها نشوند و الكترودها بتوانند به راحتي روي قطعات بنشينند.
پهناي قطعات قابل جوشكاری با نقطه جوش بستگي به طول فكهاي ماشين دارد و معمولا از 5 تا 50 اينچ تغيير ميكند.
محدوده ضخامت قطعات نيز بين 0.008 تا 1.25 اينچ ميباشد.
كيفيت و عيوب جوشکاری نقطه جوش
براي انجام يك عمليات نقطه جوش موفق بايد ماشين را به درستي تنظيم نمود. عواملي نظير نيروي اعمالي الكترود بر قطعه كار، دماي الكترود، جنس الكترود، جريان الكتريكي و تميز بودن سطوح الكترودها و قطعه كار، بر كيفيت نقطه جوش موثر ميباشند.
جدول 36- عيوب رايج در جوشكاری نقطه جوش به همراه علل احتمالي و اثرات نامطلوب آنها
اثرات نامطلوب | علل احتمالي | عيب | ||
كاهش استحكام نقطه جوش ظاهر بد | –
– |
فرم نامناسب الكترود يا نيروي نادرست آن
حرارت زياد به هنگام جوشكاری |
–
– |
فرورفتگي |
كاهش سطح اتصال در نقطه-جوش | – | – نيروي كم الكترود
– جريان الكتريكي زياد |
ذوب شدن موضعي | |
سوراخشدن محل نقطه جوش | – | |||
كاهش استحكام جوش | – | – ساييدگي سطح الكترود
– كثيف بودن سطح الكترود |
فرم نامنظم نقطه جوش | |
كاهش استحكام جوش كاهش عمر الكترود | –
– |
– نيروي كم الكترود
– جنس نامناسب الكترود |
عملكرد نادرست الكترود | |
كاهش استحكام خستگي احتمال افزايش خوردگي | –
– |
حرارت زياد به هنگام جوشكاری رها كردن پيش از موقع الكترود از قطعه | –
– |
ايجاد ترك و حفره در نقطه جوش |
اثرات نقطه جوش بر خواص ماده
از جمله اثرات نقطه جوش بر خواص مختلف قطعه كار، ميتوان به سخت شدن ماده، كاهش استحكام خستگي، پيچيدگي قطعه كار، نرم شدن احتمالي، ايجاد كشيدگي در قطعه كار، ايجاد ظاهر بد و كاهش مقاومت در برابر خوردگي اشاره نمود.
جدول 37- اثرات نقطه جوش بر خواص ماده
اثرات فرآيند بر خواص ماده | خواص ماده | |
احتمال سختشدن ماده | – | مكانيكي |
2- احتمال كاهش استحكام خستگي | – | |
3- احتمال پيچيدگي و اعوجاج در قطعهكار | – | |
احتمال نرمشدن ماده | – | |
ايجاد كشيدگي در قطعهكار | – | |
ظاهر بد | – | فيزيكي |
احتمال ايجاد تركهاي داخلي | – | |
ايجاد تخلخل و اسفنجيشدن ماده | – | |
احتمال ايجاد تركهاي سطحي | – | |
احتمال كاهش مقاومت در برابر خوردگي | – | شيميايي |
عوامل موثر در نتيجه فرآيند
عوامل موثر در نتيجه عمليات نقطه جوش عبارتند از:
- قابليت هدايت الكتريكي و حرارتي الكترودها
- جريان الكتريكي
- جنس و فرم الكترودها
- نيروي اعمالي الكترودها به هنگام جوشكاری
- زمان جوشكاری
- فاصله بين نقطه جوشها
- جنس قطعه كار
جوشكاری زيرپودري
در عمليات جوشكاری زيرپودري Submerged Arc Welding، حرارت مورد نياز براي ذوب و امتزاج سيم جوش و قطعه كار، از يك قوس الكتريكي كه بين سيم جوش و قطعه كار برقرار ميشود، به وجود ميآيد. سيم جوش اين فرآيند نقش الكترود را نيز ايفا ميكند. محافظت از ناحيه جوشكاری و گرده جوش ايجاد شده، بر عهده پوشش ضخيمي از دانه هاي جامد فلاكس است كه روي ناحيه جوشكاری را ميپوشاند و به همين دليل به اين فرآيند، جوشكاری زيرپودري اطلاق ميشود.
ويژگيهاي فرآيند جوشكاری زيرپودري
- در عمليات جوش زيرپودري از يك الكترود مصرف شدني با پيشروي اتوماتيك استفاده ميشود.
- موضع جوشكاری با پودر فلاكس محافظت ميشود. مقداري از پودر در اثر حرارت به گاز تبديل ميشود.
- پودر فلاكس پس از جوشكاری به صورت يك گل جوش جامد روي گرده جوش باقي ميماند.
- سرعت جوشكاری و سرعت رسوب سيم جوش مذاب روي درز جوش در اين فرآيند بالا ميباشد.
- قطعات ضخيم را با استفاده از اين روش ميتوان با كيفيتي بسيار خوب جوشكاری نمود.
- جوشكاری زيرپودري به صورت اتوماتيك و نيمه اتوماتيك اجرا ميشود.
قابليتهاي فرآيند جوشكاری زيرپودري
طرح درز جوش در اين روش، بايد به گونهاي باشد كه بتواند پودر محافظ را در خود نگه داشته و بدين ترتيب عملكرد پودر روي سطح بهينه گردد. ضخامت قطعه كار در جوش زيرپودري معمولا بين 0.25 تا 1 اينچ ميباشد. اين محدوده ممكن است از 0.06 تا 8 اينچ نيز افزايش يابد.
كيفيت ظاهري و عيوب رايج در جوشكاری زيرپودري
سه عيب رايج در عمليات جوشكاری زيرپودري عبارتند از: ترك هاي ريز، تخلخل هاي زيرسطحي و عدم ذوب كامل منطقه جوشكاری. اين عيوب ميتوانند باعث كاهش استحكام جوش شوند. در جدول زير به تعدادي از عيوب رايج به همراه علل احتمالي و اثرات نامطلوب آنها اشاره شده است:
جدول 38- عيوب رايج در جوشكاری نقطه جوش به همراه علل احتمالي و اثرات نامطلوب آنها
اثرات نامطلوب | علل احتمالي | عيب | ||
غيرقابل قبول (جوشكاری دوباره) | – | تنشهاي مكانيكي تنشهاي حرارتي
وجود ناخالصي در عناصر آلياژيو تركيب ماده |
–
– – |
ترك |
كاهش استحكام جوش | – | آلودگيهاي سطح قطعه كارحبس شدن گاز در مذاب | –
– |
تخلخل زيرسطح |
ظاهر بد | – | جريان الكتريكي بالا | – | گرده جوش ناصاف و چيندار |
كاهش استحكام جوش | – | آلودگي سطح قطعه كار سرعت جوشكاری بالا | –
– |
عدم ذوب كامل |
ايجاد تمركز تنش | – | |||
كاهش استحكام جوش | – | حبس شدن گاز و مواد پودر محافظ در مذاب | – | وجود آخال و آلودگي در جوش |
اثرات جوشكاری زيرپودري بر خواص ماده
جدول 39- اثرات جوشكاری زيرپودري بر خواص ماده
اثرات فرآيند بر خواص ماده | خواص ماده | |
احتمال سخت شدن ماده | – | مكانيكي |
2- تردید كاهش استحكام خستگي | – | |
3- شایدی ايجاد انقباض | – | |
احتمال نرم شدن ماده | – | |
ايجاد پيچيدگي قطعه كار | – | |
ظاهر بد | – | فيزيكي |
احتمال ايجاد ترك و تخلخل در ماده | – | |
احتمال كاهش مقاومت خوردگي در ناحيه جوشكاری شده | – | شيميايي |
جنس قطعه كار
اغلب فلزات را به اين روش ميتوان جوشكاری كرد ولي معمولا فولاد نرم، چدن و فولاد زنگ نزن، به دليل قابليت جوشكاری بهتر نسبت به ديگر فلزات، نتيجه بهتري در جوشكاری زيرپودري از خود نشان ميدهند.
جنس سيم جوش و پودر محافظ
در ادامه به جدول مشخصات سيم جوش ها توجه نماييد:
جدول 40- جنس سيم جوش و پودر محافظ در جوشكاری زيرپودري
كد سيم جوش | وضعيت جوشكاری | پودر محافظ |
E6010 | افقي | سديم با سلولز بالا |
E6013 | بالاي سر | پتاسيم با تيتانيوم اكسيد بالا |
E6027 | گوشه هاي افقي | پودر با اكسيدآهن بالا |
E7014 | عمودي، افقي، بالاي سر | پودر آهن و تيتانيوم اكسيد |
E7048 | عمودي، پايين، بالاسر، افقي | پودر آهن، پتاسيم كم هيدروژن |
عوامل موثر در نتيجه فرآيندجوشکاری زیرپودری
عوامل موثر در نتيجه عمليات جوشكاری زيرپودري عبارتند از:
- جريان و ولتاژ جوشكاری
- نوع جريان الكتريكي
- پوشش پودر در ناحيه جوشكاری
- تميز بودن سطح قطعه كار
- سرعت جوشكاری و سرعت رسوب مذاب
- جنس الكترود
- ميزان هدايت الكتريكي قطعه كار
- طرح اتصال
- جنس قطعه كار و ويژگيهاي
لحيم كاري مدارهاي الكترونيكي
در اين روش لحيم كاري، فيبر مدار چاپي از لحيم مذاب عبور كرده و به اين ترتيب روي خطوط مدار و دنباله قطعات الكترونيكي، لايه اي از لحيم مينشيند و بدين ترتيب قطعات روي مسيرهاي خاصي به هم متصل ميشوند. موج لحيم مذاب با استفاده از يك پمپ به وجود ميآيد.
ويژگيهاي فرآيند
- عمليات لحيم كاري تميز و قابل اطمينان ميباشد.
- يك روش لحيم كاري اتوماتيك محسوب ميشود.
- مازاد لحيم و فلاكس را دوباره ميتوان استفاده نمود.
- بعد از لحيم كاري بايد مدار حاصل را از نظر درستي اتصالات و عملكرد، بازرسي و آزمايش نمود.
- سرعت لحيم كاري و بهرهوري در اين عمليات بالا ميباشد.
تركيب ماده لحيم كاري
ماده لحيمكاري، تركيبي از قلع، سرب و اندكي آنتيموان است. اين ماده معمولا آلياژي حاوي 50 درصد قلع، 49.5 درصد سرب و 0.5 درصد آنتيموان است
قابليتهاي فرآيند
اين فرآيند به لحيمكاري اتوماتيك مدارات الكترونيكي اختصاص دارد. ابعاد فيبر مدار چاپي تنها محدوديت عملياتي اين فرآيند محسوب ميشود و اندازه ماشين را تعيين ميكند
كيفيت و عيوب لحيم كاري اتوماتيك
كيفيت لحيمكاري در اين روش به حرارت پيشگرم، حرارت لحيم مذاب و تميز بودن سطوح قبل از لحيم كاري (كيفيت فلاكس) بستگي دارد. در جدول زير تعدادي از عيوب رايج در اين روش را مشاهده ميكنيد:
جدول 41- تعدادي از عيوب رايج در روش لحيم كاري اتوماتيك
اثرات نامطلوب | علل احتمالي | عيب | ||
كاهش هدايت الكتريكي | – | تنش هاي مكانيكي | ترك | |
كاهش استحكام خطوط و اتصالات كاهش هدايت الكتريكي | –
– |
آلودگي سطوح لحيمكاري كمبود فلاكس پيش گرم ناگهاني | –
– – |
حفره يا تخلخل |
احتمال ايجاد تنش مكانيكي
عدم تحمل جريان نامي مدار در صورت نازك بودن ضخامت لحيم |
–
– |
دماي نامناسب لحيم مذاب سرعت نادرست نوار نقاله | –
– |
ضخامت نادرست لحيم |
احتمال ايجاد اتصال كوتاه بين خطوط و قطعات | – | |||
خرابي كل مدار | – | وجود آلودگي در لحيم مذاب | – | هدايت الكتريكي ضعيف مدار |
اثرات لحيم كاري اتوماتيك بر خواص ماده
جدول 42- اثرات لحيم كاري اتوماتيك بر خواص ماده
اثرات لحيم كاري بر خواص ماده | خواص ماده | |
جدايش لايه هاي فيبر مدار چاپي | – | مكانيكي |
ايجاد شكنندگي در فيبر | – | |
پيچيدگي و اعوجاج در بعضي قطعات مدار | – | |
اثرات اندكي دارد. | – | فيزيكي |
اثرات نامطلوب فلاكسهاي خورنده | – | شيميايي |
عوامل موثر در نتيجه فرآيند
عوامل موثر در قابليت لحيم كاري يك قطعه كار عبارتند از:
- تميز بودن قطعات
- دماي قطعه كار
- ضخامت مناسب لحيم
- هدايت گرمايي قطعه كار
- ميزان انبساط و انقباض قطعه كار
- نوع لحيم و ويژگيهاي آن
تجهيزات عمومي مورد نياز در جوشکاری
الكترودهاي جوشکاری
الكترود مفتولي فلزي است كه دور تا دور آن با مواد شيميايي پوشش داده شده است و ضمن هدايت جريان از انبر به فلز پايه، پركننده درز جوش و تامين كننده مواد آلياژي ميباشد. الكترود را ميتوان به چهار صورت دسته بندي كرد:
- ازنظر قطر
- ازنظر طول
- از نظر مغزي فلزي
- ازنظر پوشش
الكترودها در قطرهاي 1 تا 10 ميليمتر وجود دارند اما پركاربردترين آنها عبارتند از 2، 3.2، 4 و 5 ميليمتري. الكترودها درطولهاي 20 تا50 سانتيمتري وجود دارند. الكترود ازنظر مغزي فلزي به الكترودهاي فولادي، آلياژي، چدني، الكترود فلزات رنگين و الكترود زغالي تقسيم بندي ميشوند. الكترود ها از نظر پوشش به الكترودهاي روتيلي، قليايي، سلولزي، اسيدي و مركب تقسيم ميشوند.
مواد تشكيل دهنده پوشش الكترودها ميتوانند آهك، اكسيد سديم، سلولز، روتيل، آزبست، خاكرس، دياكسيدتيتانيوم و مقداري ديگر از مواد گوناگون باشند.
انتخاب صحيح الكترود براي جوشکاری بستگي به نوع قطب و حالت درز جوش دارد. مثلاً يك درز V شكل با زاويه كمتر از 40 درجه با ضخامت زياد حداكثر با قطر 1 اينچ كه معادل 2 ميليمتر است براي رديف اول گرده جوش استفاده ميگردد تا كاملاً در عمق جوش نفوذ نمايد. ولي چنانچه از الكترود با قطر بيشتر استفاده شود مقداري تفاله در ريشه جوش باقي خواهد ماند كه قدرت و استحكام جوش را تقليل ميدهد.
نکته
بايستي توجه داشت كه هميشه قطر الكترود از ضخامت فلز جوشکاری كمتر باشد. هر چند كه در بعضي از كارخانجات توليدي عدهاي از جوشكاران، الكترود با ضخامت بيشتر از ضخامت فلز را به كار ميبرند. اين عمل بدين جهت است كه سرعت كار زيادتر باشد ولي انجام آن احتياج به مهارت فوق العاده جوشكار دارد. همچنين انتخاب صحيح قطر الكترود بستگي زياد به نوع قطب ( + يا – ) و حالت درز جوش دارد. مثلاً اگر يك درز V شكل با زاويه كمتر از 40 درجه باشد بايستي حداكثر از الكترود با قطر پنج شانزدهم اينچ براي رديف اول گرده جوش استفاده كرد تا كاملاً بتوان عمق درز را جوش داد. چنانچه از الكترود با قطر زيادتر استفاده شود مقداري تفاله در جوش باقي خواهد ماند كه قدرت و استحكام جوش را به طور قابل ملاحظه اي كاهش خواهد داد.
اطلاعات پاكت الكترود
مطابق استاندارد، پاكت ها و كارتن هاي الكترود بايستي علامتها و نوشتههايي داشته باشند كه حتيالمقدور مصرف كننده را در دسترسي به كيفيت مطلوب جوش راهنمائي و ياري نمايند. در روي پاكت الكترود علاوه بر نام كارخانه سازنده، نوع جنس نيز درج ميشود كه براي مصرف صحيح حائز اهميت است. هر پاكت الكترود بايستي علاوه بر اسم تجاري الكترود، طبقه بندي آن الكترود را حداقل طبق يكي از استانداردهاي مهم بيان نمايد. براي آگاهي از طول زمان ماندگي الكترود در كارخانه، بازار يا انبار، شماره ساخت يا تاريخ توليد روي پاكت نوشته يا مهر زده ميشود. قطر سيم مغزي الكترود، مصرف كننده را در كاربرد صحيح آن با توجه به ضخامت فلز، زاويه سيار، ترتيب پاس و غيره راهنمايي ميكند.
نوع جريان برق (جريان دائم يا جريان متناوب لازم يا هر دو) و در جريان دائم نوع اتصال قطبي، بايستي به صورت عبارت يا علامت روي پاكت درج شود. حالت يا حالاتي از جوشکاری كه اين الكترود در آن حالت يا حالات مناسب است روي پاكت بيان ميشود. درج حدود شدت جريان برق بر حسب آمپر، جهت انتخاب اوليه ضروري است. وزن الكترودها يا تعداد الكترود داخل هر بسته روي پاكت يا برچسب آن درج ميشود. نوشتن مواردي كه در بالا به آن اشاره شد، روي پاكت مطابق با بيشتر استانداردها اجباري است.
ادامه
همچنين خواص مكانيكي و شيميايي، وضعيت ذوب و كيفيت، نحوه نگهداري و انبار كردن، درجه حرارت خشك كردن، موارد استعمال به خصوص و پارهاي توصيه هاي ديگر در روي پاكت براي آگاهي مصرف كننده چاپ شده و يا مهر زده ميشود.
الكترودهائي كه در جوش اتصال فولاد به كاربرده ميشوند، مفتولهاي مغزي با آلياژ يا بدون آلياژ دارند كه جريان جوش را هدايت ميكنند. شعله برق بين قطعهكار و سر آزاد الكترود ميسوزد و الكترود به عنوان يك ماده اضافي ذوب ميشود. الكترودهاي نرم شده داراي علائم اختصاري بوده كه روي بسته بندي آنها نوشته شده است. علائم اختصاري تمام نكات مهمي كه در به كار بردن آن الكترود بايد مراعات شوند را نشان ميدهند.
مشخصات الكترودها
مشخصات الكترودها با يك سري اعداد مشخص ميگردند. اعداد مشخصه به ترتيب زير ميباشد:
به عنوان مثال E 60 10 علامت اول از سمت چپ در علائم الكترود مشخص مينمايد كه اين الكترود براي جوشکاری برق استفاده ميشود. بعضي از الكترودهاي پوشش دار در جوشکاری با اكسي استيلن استفاده مي شوند. علامت دوم يعني عدد دو رقمي بعد، مشخصه فشار كشش گرده جوش بر حسب پاوند بر اينچ مربع بوده بايستي آن را در 1000 ضرب نمود يعني فشار كشش گرده جوش اين نوع الكترود 60000 پوند بر اينچ مربع يا درحدود 400 مگاپاسكال است. علامت سوم حالات جوش را مشخص ميكند كه هميشه اين علامت 1 يا 2 يا 3 ميباشد. الكترودهايي كه علامت سوم آنها 1 باشد در تمام حالات جوشکاری ميتوان از آنها استفاده كرد. الكترودهايي كه علامت سوم آنها عدد 2 باشد در حالت سطحي و افقي مورد استفاده قرار ميگيرند.
علامت سوم
الكترودهايي كه علامت سوم آنها 3 باشد تنها در حالت افقي مورد استفاده قرار ميگيرند. علامت چهارم خصوصيات ظاهري گرده جوش و نوع جريان را مشخص مينمايد كه اين علائم از 0 شروع و به 6 ختم ميگردند. چنانچه علامت چهارم يا آخر صفر باشد موارد استعمال اين الكترودها تنها با جريان مستقيم و با قطب معكوس ميباشد. نفوذ اين جوشکاری زياد و شكل مهره هاي جوش آن تخت و درجه سختي گرده جوش تقريباً زياد ميباشد.
علامت چهارم
چنانچه علامت چهارم يك باشد موارد استعمال اين الكترود با جريان مسقيم يا متناوب ميباشد. شكل ظاهري جوش اين الكترود صاف و در شكافها و درزها كمي مقعر و درجه سختي جوش كمي زيادتر از گرده اول است. اگر علامت چهارم 2 باشد موارد استعمال الكترود با با جريان مسقيم يا متناوب ميباشد. نفوذ جوش متوسط و درجه سختي جوش كمي كمتر از دو گروه قبل ميباشد. نماي ظاهري آن محدب است. اگر علامت چهارم 3 باشد اين الكترود را ميتوان با جريان متناوب يا جريان مستقيم به كار برد. درجه سختي گرده جوش اين الكترود كمتر از دو گرده اول و دوم و كمي بيشتر از گرده سوم ميباشد و نيز در داراي قوس الكتريكي خيلي آرام و نفوذ كم و شكل مهرههاي آن در درزهاي شكل محدب ميباشد.
اگر علامت چهارم 4 باشد اين الكترود را ميتوان با جريان مسقيم يا متناوب به كار برد. موارد استعمال اين الكترود براي شكافهاي عميق يا در جايي كه چندين گرده جوش به روي هم لازم است ميباشد. چنانچه علامت آخر 5 باشد مشخصه اين علامت اين است كه فقط جريان مستقيم مورد استفاده قرار ميگيرد و موارد استعمال آن در شكاف هاي باز و عميق است. درجه سختي گرده جوش اين الكترود كم و داراي قوس الكتريكي آرامي است و پوشش شيميايي آن از گروه پوشش الكترودهاي بازي است. چنانچه علامت آخر 6 باشد خواص و مشخصه آن مطابق گروه قبل است با اين تفاوت كه با جريان متناوب مورد استفاده قرار ميگيرد.
ميز مخصوص جوشکاری
ميز مخصوص جوشکاری مجهز به گيره و بازويي است كه ميتواند قطعات كوچك مورد جوشکاری را در وضعيت دلخواه نگه دارد. اين ابزار سبب سهولت در انجام كار و همچنين افزايش سرعت جوشکاری ميگردد.
سيستم تهويه
در ايستگاه هاي جوشکاری به منظور تهويه و تخليه دود و گرد و غبارهاي ناشي از جوشکاری ، از يك سيستم مكنده استفاده شده تا ريه هاي جوشكار در اثر استنشاق گازهاي سمي ناشي از جوشکاری و ديگر آلاينده هاي موجود در محيط، آسيب نبيند.
گيره ها و ديگر ابزارها
اتصالات و الكترودگيرها نيز با ساختمانهاي متفاوت طراحي شدهاند و فنر الكترودگير را نبايد حرارت داد و بهتر است وقتي الكترود به طول 5 سانتيمتر باقي ميماند، آن را تعويض نمود كه صدمه به انبر جوشکاری نزند. گيرههاي مختلف اتصال به ميز، جهت اتصال صحيح براي عبور جريان، يكي از موارد مهم در جوشکاری برق ميباشد. در دنياي صنعتي فعلي مسئله وسائل اندازهگيري دقيق بسيار مهم ميباشد و حتي وسايل اندازهگيري الكترونيكي جهت اين امر ساخته شدهاند. ابزارهايي نظير چكش گلزني، برس سيمي، ماشين سنگزني، قيود و ابزارهاي نگهدارنده و گيره هاي كمكي از جمله ابزارهاي موجود مورد نياز در ايستگاه هاي جوشکاری ميباشند. چكش جوش براي برطرفنمودن گل جوش ميباشد و برس براي تميز نمودن سطح جوش از گل جوش جهت جوشکاری بعدي است.
قفسه ها و صندوقچه هاي نگهداري الكترود جوشکاری
ايستگاه هاي جوشکاری بايد داراي تجهيزاتي براي نگهداري الكترودها، مانند قفسه ها و حامل هاي الكترود باشند. اين قفسه ها بايد بر اساس اندازه و نوع الكترودها نامگذاري شده و به دور از رطوبت نگهداري شوند.
مشعل هاي جوشکاری
وظيفه مشعل تنظيم اختلاط گاز سوخت و اكسيژن به اندازه معين ميباشد كه آن را با سرعت كمي بيشتر از سرعت احتراق از دهانه خود خارج مينمايد. مشعلها بر دو نوع ميباشند: مشعل فشار مساوي و مشعل انژكتوري يا فشار ضعيف. در مشعل انژكتوري اكسيژن با فشار 3 اتمسفر از سوراخهاي ريز انژكتور مانند و دايرهاي خارج شده و گاز سوخت را كه در روزنه وجود دارد با خود بهدرون محفظه اختلاط ميكند و پس از مخلوط شدن به نسبت مساوي از سر مشعل خارج ميسازد كه به مشعل فشار ضعيف يا انژكتوري معروف ميباشد. در نوع ديگر مشعل فشار مساوي اكسيژن و گاز سوخت با فشار مساوي وارد محفظ اختلاط گرديده و با هم مختلط ميشوند و هر دستگاه چند لوله اختلاط كننده با سر مشعل مربوطه دارد كه از استيلن موجود در لوله هاي فشار قوي استفاده كرده و با تعويض سر مشعل شعله هاي مختلفي ايجاد مينمايد.
رگلاتور
فشار گاز در كپسول اكسيژن در حدود 150 اتمسفر و در كپسول استيلن 15 اتمسفر ميباشد و جوشکاری با اين فشارهاي زياد امكانپذير نيست. به اين جهت بايستي فشار كپسول را كاهش داده و به فشار گاز تبديل نمود. فشار گاز با بزرگي و كوچكي سرمشعلي كه براي جوشکاری به كار ميرود، تغيير ميكند و مقدار آن معمولا براي اكسيژن 5/0 الي 4 اتمسفر و براي استيلن 2/0 الي 1 اتمسفر ميباشد. فشار گاز در تمام مدت جوشکاری ثابت و يكسان ميباشد. عمل كاهش و تنظيم فشار گاز كپسول ها به وسيله رگلاتور انجام ميگيرد. رگلاتور از لحاظ ساختمان مكانيكي بر دو نوع است:
- رگلاتور انژكتوري
- رگلاتور سوپاپي
رگلاتورهاي انژكتوري بيشتر متداول بوده كه بدنه آن از برنج ساخته شده و داخل رگلاتور از چند فنر و يك ديافراگم و انژكتور تشكيل شده است. اگر پيچ تنظيم فشار در جهت عقربههاي ساعت پيچانده شود فشار كار و در نتيجه مقدار گاز زياد ميگردد و اگر گاز مصرف نگردد جريان آن به خودي خود قطع ميگردد و هم چنين فشار كپسول هر مقدار باشد رگلاتور وظيفه خود را به نحو احسن انجام ميدهد. رگلاتور سوپاپي نيز داراي اصول كاري مانند رگلاتور انژكتوري ميباشد با اين تفاوت كه در آن به جاي انژكتور سوپاپ به كار رفته است. اجزا مختلف اين رگلاتور نيز مانند رگلاتور انژكتوري ميباشد و ميله سوپاپ آن از فولاد بسيار عالي ساخته ميشود.
فشارسنج ها
يكي از حساسترين قسمتهاي جوشکاری، دستگاههاي فشارسنج براي اكسيژن و هيدروژن و ديگر گازها ميباشد. فشارسنجهاي متفاوتي براي اكسيژن – استيلن و ساير گازها پيشبيني شدهاند كه در روي كپسول ها نصب ميگردند.
ماشينهاي جوشکاری
ماشينهاي جوشکاری به دو نوع ماشينهاي جوشکاری با جريان مستقيم و متناوب تقسيم ميشوند كه به شرح زير ميباشند:
- ماشينهاي جوشکاری با جريان مستقيم ماشينهايي ميباشند كه در آنها قوس الكتريكي با جريان مستقيم ايجاد ميشود.
- ماشينهاي جوشکاری با جريان متناوب ماشينهايي ميباشند كه در آنها قوس الكتريكي با جريان متناوب ايجاد ميشود.
تجهيزات ايمني مورد نياز در جوشکاری
رعايت نكات ايمني، خود يكي ديگر از مشكلات عظيم جوشکاری است، به طوري كه انفجار يك كپسول مانند يك بمب ميتواند جان صدها نفر را به خطر اندازد، در حاليكه مثلاً در يك كارگاه تراش و ريختهگري، خطرات تا اين حد بالا نيستند. كوچكترين بوي گاز ناشي از عدم اتصالات صحيح و اصولي، ممكن است جان عدهاي را در معرض خطر قرار دهد. وسايل ايمني در جوشکاری به سه دسته وسايل ايمني سر، بدن و سيستم تنفسي جوشكار تقسيم ميشوند.
وسايل ايمني سر جوشكار
با توجه به وجود اشعه هاي ماوراء بنفش و مادون قرمز موجود در جوشکاری قوس الكتريكي و آثار مضر آنها بر پوست و چشم جوشكار و اطراف نزديك محل جوشکاری، بايد از ماسك هاي كلاهي و عينك هاي ايمني استفاده نمود. اين تجهيزات همچنين از سر جوشكار در برابر پاشش و ريزش قطرات مذاب به خصوص در هنگام جوشکاری در وضعيت سقفي، محافظت ميكنند. جوش برق به علت جرقه قوي و اشعه ماوراء بنفش به شدت به چشم صدمه زده و چندين مرتبه نگاه كردن با چشم غيرمسلح كافي است كه عوارض و درد چشم را به همراه داشته باشد. جهت رفع اين عارضه ميتوان از كمپرس آب سرد و غيره استفاده كرد.
درجه بندی
شيشه هاي عينكي در جوشکاری برق شماره گذاري شده و بر طبق جدول بايستي انتخاب شوند و طوري باشند كه به سختي بتوان نور يك چراغ را تشخيص داد. اين عينكها به صورت انواع ماسك هاي دستي، صورتي و كلاهي ساخته ميشوند. براي راحتي كاركردن و نيز كار در محلهاي سخت، از انواع ماسكها با تجهيزات مختلف استفاده ميگردد. نور شديدي كه به وسيله شعله اكسي استيلن توليد ميشود چنانچه با چشم غيرمسلح به آنها نگاه كنيم سبب صدمه زدن به بافتهاي چشم ميگردد.
بنابراين بايد هميشه يك عينك مناسب با شيشه رنگي كه مورد تائيد متخصص است به كار برد و مقدار تيرگي عينك بايد طوري باشد كه نور به اندازه لزوم جهت ديدن كار از آن عبور كند. چنانچه پس از برداشتن عينك از چشم نقاط سفيدي در حال جنب و جوش در برابر چشم ديده شوند نشان دهنده آن است كه شيشه همه نورهاي مضر را جذب نميكند.
وسايل ايمني بدن جوشكار
استفاده از دستكش و پيشبند چرمي در هر نوع جوش برق و گاز ضروري است. زيرا ذرات مذاب فلز بر روي بدن و سر و صورت جوشكار پرتاب شده و سبب سوختگي ميگردد. توجه نمائيد به هيچ وجه در حين جوشکاری از لباسهاي پشمي استفاده نكنيد. استفاده از لباس كار ايمن جهت محافظت از بدن در برابر گدازه هاي داغ، گل جوش، حرارت و همچنين اشعه-هاي مضر، ضروري ميباشد. لباس كارهاي از جنس كتان با بافت محكم و رنگ تيره، براي اين منظور گزينه بسيار مناسبي مي باشند. در بعضي موارد، استفاده از دستكشهاي تمام چرمي و پيشبندهاي بلند نيز توصيه ميگردد.
وسايل ايمني تنفسي
به منظور جلوگيري از استنشاق گردوغبار، دودها و گازهاي سمي جوشکاری، از دو روش يا ابزار ميتوان بهره جست. نخست از ماسك هاي فيلتردار و ديگري از هود يا مكنده هاي فشار قوي در نزديكي محل كار براي تخليه دود و گرد و غبار و همچنين تهويه مناسب محل جوشکاری.
كنترل كيفيت و بازرسي جوشکاری
طبق طبقه بندي، استانداردهاي مديريت كيفيت جوشکاری جزء فرآيندهاي ويژه طبقه بندي شده است كه اين نشان دهنده اين است كه براي كنترل كيفيت و تضمين كيفيت اين فرآيند ويژه ميبايد، پيشبيني هاي خاصي انجام داد. به اين منظور پيش از عمليات جوشکاری تمام پارامترها دخيل در فرآيند شامل مواد اوليه، دستگاه و تنظيمات آن، مواد مصرفي و جوشكار بر طبق استاندارد ايزو 3834 مورد ارزيابي و بررسي و تاييد قرار ميگيرند.
به منظور حصول جوشي با كيفيت و عاري از عيب، كليه عوامل جوشکاری بايد در مراحل متعددي مورد بازرسي و كنترل قرار گيرند. در صورت انجام اين امر توسط ناظران و يا بازرسان كنترل كيفيت جوش، ميتوان تا حد زيادي از بروز عيوب در پايان كار جلوگيري به عمل آورد و هزينه هاي تعمير، رفع عيوب و دوباره كاري ها را به حداقل رساند. مراحل بازرسي در جوشکاری به سه بخش تقسيم ميشوند:
- بازرسي قبل از شروع كار
- بازرسي در حين انجام كار
- بازرسي پس از اتمام كار
بازرسي جوشکاری قبل از شروع كار
اين فرآيند به منظور مهيا ساختن مقدمات جوشکاری صورت پذيرفته و شامل مراحل زير ميباشد:
- مطالعه و بررسي نقشهها و مشخصات فني و استانداردهاي مرتبط با آنها
- انتخاب و ارزيابي روش جوشکاری مبتني بر استاندارد و مطابق نقشهها و مشخصات كار
- انتخاب مصالح و مواد مصرفي و بررسي و تست آنها براي اطمينان بيشتر و نهايي
- بررسي تجهيزات جوشکاری نظير دستگاههاي جوشکاری و برش، كابلها، شيلنگها، كپسولها، اتصالات، قيدها و بندها و غيره
- بررسي ايمني محل و تجهيزات جوشکاری
- انجام تست مهارت
بازرسي جوشکاری در حين انجام كار
پس از حصول اطمينان و تاييد نهايي مراحل بازرسي قبل از شروع كار كه بدان پرداخته شد، مرحله بعدي بازرسي در حين انجام كار بايد صورت پذيرد كه به شرح زير ميباشد:
- بازرسي قطعات و اتصالات آماده شده، بازرسي جهت حصول اطمينان از عدم وجود آلودگي و كثيفي
- بازرسي شكل و ابعاد درزها و شيارها و نحوه فيتشدن و وضعيت استقرار آنها نسبت به يكديگر با توجه به نقشه
- بازرسي طرز قرار گرفتن قطعات در موقعيتهاي مورد نظر و همچنين قيدها و گيرههاي نگهدارنده آنها
- چك كردن ابعاد پشتبندها و قرارگرفتن صحيح آنها در محل خود
- چك كردن جوشهاي موقتي، گيرهها، قيدها و قطعات تقويتي بر اساس و مطابق قواعد فني مربوطه
- تاييد صلاحيت جوشكار در هر مرحله با استفاده از آزمايش و تاييد جوشکاری انجام شده
بازرسي جوشکاری پس از اتمام كار
اين نوع بازرسي به شيوههاي مختلفي مانند آزمون تستهاي غيرمخرب صورت ميپذيرد. تست هاي غيرمخرب به تستهايي اطلاق ميشود كه بدون تخريب يا تغيير در خواص فلز جوش يا قطعه كار صورت ميپذيرند.
بازرسي چشمي
بازرسي چشمي Visual test از رايجترين و مهمترين روشهاي بازرسي غيرمخرب براي مواد خام، محصولات در حال ساخت و محصولات ساخته شده ميباشد. در اين روش ابتدا با برس سيمي سطح را از سرباره و پوسته پاك ميكنند چرا كه اين كار از پيش شرط هاي بازرسي چشمي است و سطح جوش بايد به وضوح ديده شود. براي اين كار ميتوان از ذره بيني با بزرگنمايي در حدود 10 برابر استفاده نمود. انواع عيوبي كه ميتوان با چشم مشاهده نمود عبارتند از:
- عيوب سطحي جوش مانند تركهاي سطحي، تخلخل سطحي، بريدگي كنارههاي جوش، سوختگي فلز مبنا، سنگزدن اضافي و جوشهاي غيريكنواخت
- نادرستي شكل و انحرافات در اندازه جوش
- تغييرشكلهاي ناشي از جوشکاری مانند تابيدگي و موجدار شدن و كمانش و غيره
در اين بازرسي تنها عيوب ماكروسكوپي قابل تشخيص ميباشند.
آزمايش با مايع نافذ Penetrant test
اين روش براي ترك هاي زيرسطحي كه به چشم نميآيند مورد استفاده قرار ميگيرد. روي درز جوش را با قلم مو به مايع رنگيني كه عموما قرمز ميباشد و خاصيت نفوذ زيادي داشته باشد، آغشته مينمايند. اين مايع حتي در ترك هاي خيلي ريز و سطوح متخلخل نيز نفوذ ميكند. مدتي قطعه مورد آزمايش را به حال خود ميگذارند تا مايع در تمام سوراخها و ترك هاي گرده جوش خوب نفوذ كند. بعداً اضافه مايع را پاك ميكنند، چنانچه گرد يا گچ را روي سطح بپاشيم ترك ها و سوارخ ها بهتر ديده ميشوند. ضمناً چون مايع قابليت نفوذ خوبي دارد از ترك ها و سوراخ ها نفوذ كرده و نقاطي را در طرف ديگر جوش نشان ميدهد. اين آزمايش را ميتوان براي تمام فلزات انجام داد. انواع متداول مايعات نافذ عبارتند از:
- نفت سفيد كه از پودر گچ به عنوان ظاهركننده در آن استفاده ميشود.
- رنگ هاي نافذ (عموما قرمز) كه در نور معمولي و با چشم غيرمسلح قابل رويت ميباشند.
- نافذهاي فلورسنت كه توسط نور ماوراء بنفش قابل رويت ميباشد.
آزمايش مغناطيسي جوش Magnetic test
براده يا پودر آهن را با پارافين مخلوط كرده روي گرده جوش ميمالند. قطعه كار را در يك حوزه مغناطيسي قوي قرار مي- دهند. چنانچه سطح جوش تركخوردگي داشته باشد ذرات ريز براده هاي آهن در لبه هاي ترك جمع شده و مانند تارموئي سياه به چشم ميخورند. گاهي از پودرهاي مخصوص براي آزمايش مغناطيسي استفاده ميكنند. بايد دقت كرد كه سطح جوش كاملاً صاف و تميز باشد تا از آزمايش نتيجه خوب به دست آيد.
روش ديگر آزمايش مغناطيسي اين است كه موم را توسط كاغذ مومي روي كار ماليده و برادههاي آهن را روي كار ميپاشند. مغناطيس را به آن نزديك كرده تمركز برادههاي آهن محل ترك يا تفاله محبوس شده را نشان ميدهد. مزيت اين روش نسبت به روشهاي ديگر اين است كه سطح كار احتياج به صاف كردن گرده جوش ندارد. آزمايش مغناطيسي فقط تركهاي سطحي را نشان ميدهد و براي فلزاتي كه خاصيت مغناطيسي دارند استفاده ميشود.
بازرسي جوشکاری با امواج التراسونيك
در اين آزمايش امواج التراسونيك را كه به وسيله دستگاه مخصوص ايجاد ميشود از محل جوش عبور ميدهند و چنانچه در مسير امواج ترك يا مك يا سرباره هاي جوش وجود داشته باشد دستگاه محل آن را نشان ميدهد و درحالي كه در نقاطي كه جوش سالم است امواج گذشته و منعكس نميشود.
راديوگرافي
قطعه جوش داده را مقابل اشعه ايكس يا گاما قرار داده و پشت محل جوش داده شده را كاغذ عكاسي قرار ميدهند (مانند عكسبرداريهاي طبي). در موقع عبور اشعه از محل جوش چنانچه ترك يا درز وجود داشته باشد روي كاغذ حساس عكاسي كاملاً مشخص ميشود زيرا اشعه ايكس و گاما از غالب اشياء عبور مينمايند. براي اين منظور دستگاهي مفصل پيشبيني شده است.
عيوب متداول در جوشکاری
پيچيدگي (Torsion) و تغيير ابعاد يكي از مشكلاتي است كه در اثر اشتباه طراحي و تكنيك عمليات جوشکاری ناشي ميشود. با فرض اجتناب از ورود به مباحث تئوريك تنها به اين مورد اشاره ميكنيم كه حين عمليات جوشکاری به دليل عدم فرصت كافي براي توزيع يكنواخت بار حرارتي داده شده به موضع جوش و سرد شدن سريع محل جوش انقباضي كه ميبايست در تمام قطعه پخش ميشد به ناچار در همان محدوده خلاصه ميشود.
اين انقباض اگر در محلي باشد كه از نظر هندسي قطعه زاويه دار باشد منجر به اعوجاج زاويهاي ميشود. در نظر بگيريد تغيير زاويه اي (Angular distortion) هر چند كوچك در قطعات بزرگ و طويل چه ايراد اساسي در قطعه نهايي ايجاد ميكند. حال اگر خط جوش در راستاي طولي و يا عرضي قطعه باشد اعوجاج طولي و عرضي نمايان ميشود. اعوجاج طولي و عرضي همان كاهش طول قطعه نهايي ميباشد. اين موارد هم بسيار حساس و مهم هستند.
نوع ديگري از اعوجاج تاول زدن يا طبله كردن ميباشد. بهترين راه براي رفع اين ايراد جلوگيري از بروز آن ميباشد.
راهکار
بعضي راهكارهاي مقابله با اعوجاج عبارتند از:
- اندازه ابعاد را كمي بزرگتر انتخاب كرده و بگذاريم هر چقدر كه ميخواهد در ضمن عمليات تغيير ابعاد و پيچيدگي در آن ايجاد شود. پس از خاتمه جوشکاری عمليات خاص نظير ماشينكاري، حرارتدادن موضعي يا پرسكاري براي برطرف كردن تاب برداشتن و تصحيح ابعاد انجام ميگيرد.
- حين طراحي و ساخت قطعه با تدابير خاصي اعوجاج را خنثي كنيم.
- از تعداد جوش كمتر با اندازه كوچكتر براي بدست آوردن استحكام مورد نياز استفاده شود.
- تشديد حرارت و تمركز آن بر حوزه جوش. در اينصورت نفوذ بهتري داريم و نيازي به جوش اضافه نيست.
- ازدياد سرعت جوشکاری كه باعث كمتر حرارت ديدن قطعه ميشود.
- در صورت امكان بالا بردن ضخامت چرا كه در قطعات با ضخامت كم، اعوجاج بيشتر نمود دارد.
- تا حد امكان انجام جوش در دو طرف كار حول محور خنثي انجام شود.
- طرح مناسب لبه مورد اتصال ميتواند تا حد زيادي از ميزان اعوجاج بكاهد.
- بكار بردن گيره و بست و نگهدارنده براي مهاركردن انبساط و انقباض ناخواسته درقطعه
علل ایجاد
عوامل مهم بوجود آمدن اعوجاج عبارتند از:
- حرارت موضعي، شدت منبع حرارتي و روشي كه اين حرارت به كار رفته و همچنين نحوه سردشدن.
- درجه آزادي يا ممانعت بكار رفته براي جلوگيري از تغييرات انبساطي و انقباضي.
- تنشهاي پسماند قبلي در قطعات و اجزا مورد جوش گاهي اوقات موجب تشديد تنشهاي ناشي از جوشکاری شده و در مواردي مقداري از اين تنشها را خنثي ميكند.
- خواص فلز قطعه كار
مقالات
دورهها
[masterslider id=”1″]
.