لوبینگ یا لوبدار شدن در فرآیند سنگزنی سنترلس و محور
در این مقاله، پدیده “لوبینگ” (Lobing) در فرآیندهای سنگزنی سنترلس و محور به طور جامع مورد بررسی قرار گرفته است. از معرفی دقیق این پدیده و دلایل رخداد آن گرفته تا مزایا، معایب و روشهای جلوگیری، تمامی جنبههای مرتبط با لوبینگ پوشش داده شده است.
معرفی دقیق پدیده لوبینگ
لوبینگ به الگوی موجدار یا ایجاد انحرافات تناوبی روی سطح قطعه کار (اغلب قطعات استوانهای) اشاره دارد که در طی فرآیند سنترلس گریدینگ به وجود میآید. به جای داشتن یک سطح کاملاً گرد و یکنواخت، قطعه دارای انحرافات کوچک در نقاطی از محیط دایرهای خود است
Lobing یک نوع خطای هندسی است که در قطعات استوانهای ایجاد میشود و به شکل برآمدگیهای منظم روی سطح قطعه ظاهر میشود. تعداد این برآمدگیها (لوبها) معمولاً بین ۳ تا ۷ عدد متغیر است.
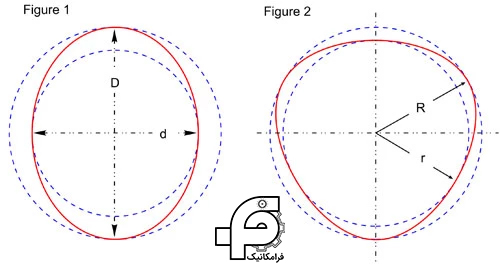
دلایل رخداد پدیده “Lobing“
دلایل متعددی برای رخداد این پدیده وجود دارد که مهمترین آنها عبارتند از:
· تنظیم ناصحیح قطعه کار در موقعیت بین چرخهای تنظیم (Regulating Wheel) و گریدینگ (Grinding Wheel):
اگر قطعه به درستی در جای خود قرار نگیرد یا تثبیت کافی نداشته باشد، ممکن است نیروهای نامتقارن وارد شده و انحرافات تناوبی (lobes) ایجاد شود.
· وضعیت و شرایط چرخ تنظیم:
چرخ تنظیم نقش کلیدی در کنترل حرکت و زاویه قطعه دارد. اگر چرخ تنظیم دچار سایش، عدم یکنواختی یا تنظیمات نادرست باشد، ممکن است باعث نوسانات و ایجاد الگوی lobing شود.
· عدم تعادل یا سایش چرخ گریدینگ:
چرخ گریدینگ که وظیفه حذف مواد را دارد، در صورت عدم تعادل یا سایش نامناسب، بهطور یکنواخت عمل نمیکند. این موضوع میتواند منجر به برداشت نامتقارن مواد از سطح قطعه و به تبع آن، ایجاد الگوی موجدار شود.
· پارامترهای فرآیند نامناسب:
سرعتهای چرخشی، نرخ پیشرفت قطعه و عمق برش از جمله پارامترهایی هستند که در صورت تنظیم نادرست میتوانند به ایجاد نوسانات در نیروهای اعمالی و نهایتاً به lobing منجر شوند.
سرعت نامناسب چرخها یا قطعه کار:
-
- عدم هماهنگی سرعت چرخ هدایتگر و قطعه کار.
- سرعتهای خیلی بالا یا خیلی پایین میتوانند باعث ایجاد ناهماهنگی در تماس قطعه و چرخ شوند.
خطا در فرایند تراز کردن (Dressing):
-
- عدم دقت در فرایند تراز کردن یا شکلدهی مجدد چرخ سنگ (dressing) که موجب توزیع غیر یکنواخت مواد ساینده میشود.
· اثرات حرارتی:
تولید حرارت در طول فرآیند گریدینگ ممکن است باعث انبساط متفاوت بخشهای مختلف قطعه شود. در صورت عدم کنترل حرارتی، اختلاف دما و انبساط میتواند منجر به تغییرات سطحی غیر یکنواخت گردد.
· ارتعاشات و فرکانسهای رزونانس:
ارتعاشات ماشینآلات یا سازههای سیستم میتوانند نوسانات را تشدید کنند. زمانی که فرکانس ارتعاشی با فرکانس طبیعی قطعه یا سیستم همراستا شود، اثرات منفی مانند lobing به وضوح ظاهر میشوند. دلایل متعددی برای رخداد این پدیده وجود دارد که مهمترین آنها عبارتند از:
· تنظیم ناصحیح قطعه کار در موقعیت بین چرخهای تنظیم (Regulating Wheel) و گریدینگ (Grinding Wheel):
اگر قطعه به درستی در جای خود قرار نگیرد یا تثبیت کافی نداشته باشد، ممکن است نیروهای نامتقارن وارد شده و انحرافات تناوبی (lobes) ایجاد شود.
وضعیت و شرایط چرخ تنظیم:
چرخ تنظیم نقش کلیدی در کنترل حرکت و زاویه قطعه دارد. اگر چرخ تنظیم دچار سایش، عدم یکنواختی یا تنظیمات نادرست باشد، ممکن است باعث نوسانات و ایجاد الگوی lobing شود.
· عدم تعادل یا سایش چرخ گریدینگ:
چرخ گریدینگ که وظیفه حذف مواد را دارد، در صورت عدم تعادل یا سایش نامناسب، بهطور یکنواخت عمل نمیکند. این موضوع میتواند منجر به برداشت نامتقارن مواد از سطح قطعه و به تبع آن، ایجاد الگوی موجدار شود.
· پارامترهای فرآیند نامناسب:
سرعتهای چرخشی، نرخ پیشرفت قطعه و عمق برش از جمله پارامترهایی هستند که در صورت تنظیم نادرست میتوانند به ایجاد نوسانات در نیروهای اعمالی و نهایتاً به lobing منجر شوند.
· اثرات حرارتی:
تولید حرارت در طول فرآیند گریدینگ ممکن است باعث انبساط متفاوت بخشهای مختلف قطعه شود. در صورت عدم کنترل حرارتی، اختلاف دما و انبساط میتواند منجر به تغییرات سطحی غیر یکنواخت گردد.
· ارتعاشات و فرکانسهای رزونانس:
ارتعاشات ماشینآلات یا سازههای سیستم میتوانند نوسانات را تشدید کنند. زمانی که فرکانس ارتعاشی با فرکانس طبیعی قطعه یا سیستم همراستا شود، اثرات منفی مانند lobing به وضوح ظاهر میشوند.
خلاصه دلایل رخداد پدیده لوبینگ
- تنظیم ناصحیح قطعه کار در موقعیت بین چرخهای تنظیم و گریدینگ
- وضعیت و شرایط چرخ تنظیم
- عدم تعادل یا سایش چرخ گریدینگ
- پارامترهای فرآیند نامناسب
- اثرات حرارتی
- ارتعاشات و فرکانسهای رزونانس
تاثیرات Lobing
- کاهش دقت ابعادی: قطعه نهایی ممکن است از نظر دقت هندسی و قطر نهایی مشکل داشته باشد.
- کیفیت سطح پایین: سطح قطعه به جای صاف و یکدست بودن، دارای موج یا ناهماهنگی است.
- سایش بیشتر در طول عمر قطعات: قطعاتی که دچار Lobing باشند، معمولاً در محیطهای کاری زودتر فرسوده میشوند.
- بازدهی پایینتر: پدیده Lobing میتواند به افزایش نرخ تولید ضایعات و نیاز به اصلاح دوباره منجر شود.
مزایا و معایب پدیده لوبینگ
مزایا:
در شرایط عادی، پدیده lobing به عنوان یک نقص محسوب میشود؛ اما در برخی موارد محدود و به عنوان یک شاخص کنترل فرآیند، میتوان به موارد زیر اشاره کرد:
- شاخص پایداری فرآیند
در برخی موارد، الگوی lobing کنترل شده میتواند نشانگر رسیدن فرآیند به یک حالت پایدار باشد و به عنوان یک معیار برای نظارت بر روند گریدینگ استفاده شود.
- مطالعه و تحلیل فرآیند
از دیدگاه پژوهشی، تحلیل الگوی lobing میتواند اطلاعات مفیدی درباره رفتار دینامیکی سیستم، شرایط سایش چرخها و تاثیر پارامترهای فرآیند ارائه دهد.
معایب:
بیشتر جنبههای این پدیده منجر به مشکلات کیفی و عملکردی قطعه میشود:
· افت دقت و تناوبی نبودن سطح:
تولید الگوی موجدار روی سطح استوانه میتواند دقت هندسی قطعه را کاهش داده و مشکلاتی در کاربردهای حساس به ابعاد ایجاد کند.
· عدم تعادل در قطعات دوار:
قطعهای که دارای lobing است ممکن است در حین چرخش دچار عدم تعادل شده و به ارتعاشات بیشتر یا خرابی اجزای متحرک منجر شود.
· افزایش هزینهها:
قطعات معیوب ممکن است نیاز به اصلاح یا تولید مجدد داشته باشند که باعث افزایش هزینههای تولید و کاهش بهرهوری میشود.
· خطر ایجاد تنشهای ناخواسته:
توزیع ناصحیح نیروها بر روی سطح قطعه میتواند باعث ایجاد تنشهای موضعی و احتمال بروز ترک یا شکست در کاربردهای نهایی گردد.
نحوه جلوگیری از پدیده لوبینگ
برای جلوگیری یا کاهش وقوع پدیده lobing، میتوان از روشها و اقدامات زیر بهره برد:
1. تنظیم دقیق قطعه کار:
اطمینان حاصل کنید که قطعه به درستی در فضای بین چرخ تنظیم و چرخ گریدینگ قرار گرفته و تثبیت شده است. تنظیمات دقیق زاویه و موقعیت قطعه نقش بسیار مهمی در جلوگیری از نوسانات دارند.
2. نگهداری و بررسی منظم چرخ تنظیم:
چرخ تنظیم باید به صورت منظم از نظر سایش، دقت سطح و تنظیمات کنترل شود. در صورت مشاهده تغییرات، لازم است به موقع تعمیر یا تعویض شود.
3. دقت در نگهداری و تعادل چرخ گریدینگ:
چرخ گریدینگ نیز باید به طور دورهای تعادلیابی و تنظیم شود. استفاده از دستگاههای نظارتی برای بررسی یکنواختی برداشتن مواد میتواند موثر باشد.
4. بهینهسازی پارامترهای فرآیند:
انتخاب سرعتهای مناسب چرخشی، نرخ پیشرفت و عمق برش به همراه کنترل دقیق دما و خنککنندگی، از بروز نوسانات و ارتعاشات جلوگیری میکند.
5. استفاده از تجهیزات کاهش ارتعاش:
نصب دستگاههای جبران ارتعاش یا استفاده از پایهها و ساختارهای تقویتی در ماشینآلات میتواند کمک کند تا ارتعاشات کاهش یافته و تاثیر منفی آنها بر روی کیفیت سطح برطرف شود.
6. کنترل حرارتی:
استفاده از سیستمهای خنککنندگی مناسب و کنترل دقیق دما در حین فرآیند گریدینگ میتواند از انبساط ناهمگون قطعه جلوگیری کرده و در نتیجه به کاهش احتمال lobing منجر شود.
7. بازرسی و کالیبراسیون منظم دستگاهها:
انجام بازرسیهای دورهای و کالیبراسیون دقیق ماشینآلات برای اطمینان از اجرای صحیح فرآیند و عدم وجود ناهماهنگی در سیستمهای حرکتی و مکانیکی بسیار حیاتی است.
8. بالانس کردن چرخها:
بالانس دورهای چرخ سنگ و هدایتگر برای کاهش ارتعاشات.
انواع لوبینگ و علل ایجاد آنها
Lobing یک نوع خطای هندسی است که در قطعات استوانهای ایجاد میشود و به شکل برآمدگیهای منظم روی سطح قطعه ظاهر میشود. تعداد این برآمدگیها (لوبها) معمولاً بین ۳ تا ۷ عدد متغیر است.
لوب 3 (Three-Lobe Pattern): – سه لوب (Three-lobing) – رایجترین نوع لوبینگ
-
- علت اصلی: نامناسب بودن زاویه مرکز – معمولاً در سرعتهای نسبی پایین اتفاق میافتد
- خصوصیات: شکل مثلثوار با سه برآمدگی یکسان
- علت اصلی: عدم تعادل نیروهای سنگزنی در سه نقطه
- راهحل: تنظیم دقیق زاویه مرکز
لوب 4 (Four-Lobe Pattern):
-
- علت اصلی: عدم تناسب سرعت بین چرخ سنگ و رگلاتور
- خصوصیات: شکل مربعوار با چهار برآمدگی منظم
- راهحل: تنظیم نسبت سرعتها و بررسی سیستم انتقال قدرت.
لوب 5 (Five-Lobe Pattern): – پنج لوب
-
- علت اصلی: ترکیبی از مشکلات ارتعاشی و تنظیمات نادرست – در سرعتهای متوسط رخ میدهد
- ویژگی خاص: پنج برآمدگی نامتقارن – معمولاً در قطعات با قطر بزرگتر دیده میشود
- راهحل: نیاز به بررسی جامع سیستم و تنظیمات مکانیکی.
لوب 6 (Six-Lobe Pattern):
-
- علت اصلی: ارتعاشات هارمونیک در سیستم
- مشخصه: شش برآمدگی نسبتاً منظم
- راهحل: نصب میراکنندههای ارتعاش و بررسی فونداسیون ماشین.
لوب 7 (Seven-Lobe Pattern):
-
- علت اصلی: ترکیب پیچیدهای از مشکلات مکانیکی و تنظیمی – در سرعتهای بالا اتفاق میافتد
- خصوصیت: هفت برآمدگی نامنظم – دامنه کمتری نسبت به سه و پنج لوب دارد
- راهحل: بازبینی کامل سیستم و احتمالاً تعویض قطعات فرسوده.
لوب 8 (Eight-Lobe Pattern):
-
- علت اصلی: فرسودگی بیش از حد یاتاقانها و گایدها
- ویژگی: هشت برآمدگی متقارن
- راهحل: تعویض یاتاقانها و بررسی سیستم روانکاری.
لوب 9 (Nine-Lobe Pattern):
-
- علت اصلی: مشکلات پیچیده سیستمی و رزونانس
- مشخصه: نه برآمدگی با الگوی خاص
- راهحل: بازطراحی پارامترهای فرآیند و احتمالاً اصلاح ساختاری.
روشهای سنگزنی شافت و تاثیر آنها بر لوبینگ
- سنگزنی سنترلس: احتمال بالای لوبینگ به دلیل نداشتن نقطه ثابت نگهدارنده و حساسیت به زاویه مرکز.
- سنگزنی محوری: احتمال کمتر لوبینگ به دلیل نگهداری از دو طرف و کنترل بهتر موقعیت.
- سنگزنی بدون مرغک داخلی (Plunge Grinding): احتمال ایجاد الگوی موجدار در صورت بالانس نبودن چرخ سنگ.
- سنگزنی شعاعی (Roll Grinding): احتمال ایجاد لوب در اثر ارتعاشات ناشی از وزن زیاد قطعه.
اندازهگیری و کنترل لوبینگ
- استفاده از دستگاه Roundness meter
- آنالیز FFT (Fast Fourier Transform)
- تنظیمات هندسی
- پارامترهای فرآیند
- بهبود سیستم
- استراتژیهای پیشگیرانه
- کنترل شرایط خنککاری
روشهای جلوگیری از لوبدار شدن شافت در فرآیندهای تولید مختلف
- تنظیم دقیق زاویه مرکز
- استفاده از سیستم ضد ارتعاش
- بالانس دقیق چرخ سنگ و رگلاژ
- تنظیم سرعت نسبی مناسب
- کنترل عمق برادهبرداری
- اطمینان از هممحوری دقیق مرغکها
- استفاده از لینت برای قطعات بلند
- کنترل لقی مرغکها
- تنظیم فشار مناسب مرغکها
- استفاده از سرعت برش و پیشروی مناسب
- انتخاب عمق براده مناسب
- استفاده از ابزار با هندسه مناسب
- کنترل ارتعاشات دستگاه
- استفاده از نگهدارندههای مناسب
- گرم و سرد کردن یکنواخت
- استفاده از فیکسچر مناسب
- کنترل دما و زمان فرآیند
- کنترل کیفیت مواد اولیه
- استفاده از سیستمهای اندازهگیری دقیق
- آموزش اپراتورها
- نگهداری منظم ماشینآلات
- پایش مداوم پارامترهای فرآیند
نکات کلیدی
- پیشگیری از لوبینگ با بازرسیهای منظم و نگهداری پیشگیرانه.
- کنترل لوبینگ با استفاده از سیستمهای مانیتورینگ آنلاین و اندازهگیریهای دورهای.
- اقدامات اصلاحی شامل تنظیم پارامترهای ماشینکاری، بهینهسازی شرایط خنککاری و تعویض قطعات معیوب.
با رعایت این نکات و استفاده از روشهای مناسب، میتوان از ایجاد لوبینگ در فرآیندهای سنگزنی و سایر فرآیندهای تولید جلوگیری کرد و کیفیت قطعات را به طور قابل توجهی بهبود بخشید.
رایجترین نوع لوبینگ در سنگ سنترلس بیشتر اتفاق میفته یا سنگ محور؟
در سنگ سنترلس (بدون مرکز) لوبینگ بسیار رایجتر است. دلایل اصلی این موضوع عبارتند از:
در سنگ سنترلس:
· قطعه کار هیچ نقطه ثابتی برای نگهداری ندارد
· تکیهگاه قطعه روی تیغه است و آزادی حرکت بیشتری دارد
· حساسیت زیاد به زاویه مرکز و تنظیمات هندسی
· تاثیرپذیری بیشتر از نیروهای سنگزنی
· معمولاً three-lobing (سه لوب) در این نوع سنگزنی رایجتر است
در سنگ محور (سیلندریکال):
· قطعه بین دو مرغک نگهداری میشود
· محدودیت حرکت قطعه به دلیل نگهداری از دو طرف
· پایداری بیشتر در حین فرآیند
· کنترل بهتر موقعیت قطعه
· احتمال کمتر ایجاد لوبینگ
البته در سنگ محور هم ممکن است لوبینگ اتفاق بیفتد، اما معمولاً دلایل آن متفاوت است:
· لقی در مرغکها
· عدم هممحوری
· ارتعاشات سیستم
· خطای بالانس چرخ سنگ
به همین دلیل، در سنگ سنترلس نیاز به کنترل و پایش دقیقتر پارامترها برای جلوگیری از لوبینگ وجود دارد.
راه های جلوگیری از لوب دار شدن شافت در فرآیند های تولید مختلف چیه؟
من روشهای جلوگیری از لوبدار شدن شافت را در فرآیندهای مختلف تولید توضیح میدهم:
در فرآیند سنگزنی:
الف) سنگ بدون مرکز (Centerless):
– تنظیم دقیق زاویه مرکز (معمولاً ۶-۸ درجه)
– استفاده از سیستم ضد ارتعاش
– بالانس دقیق چرخ سنگ و رگلاژ
– تنظیم سرعت نسبی مناسب بین چرخ سنگ و قطعه
– کنترل عمق برادهبرداری در هر پاس
ب) سنگ محور یا بین دو مرغک:
– اطمینان از هممحوری دقیق مرغکها
– استفاده از لینت برای قطعات بلند
– کنترل لقی مرغکها
– تنظیم فشار مناسب مرغکها
در فرآیند تراشکاری:
– استفاده از سرعت برش و پیشروی مناسب
– انتخاب عمق براده مناسب
– استفاده از ابزار با هندسه مناسب
– کنترل ارتعاشات دستگاه
– استفاده از نگهدارندههای مناسب برای قطعات بلند
۳. در فرآیند حرارتی:
– گرم و سرد کردن یکنواخت
– استفاده از فیکسچر مناسب
– کنترل دما و زمان فرآیند
– جلوگیری از تنشهای پسماند نامتقارن
روشهای عمومی:
– کنترل کیفیت مواد اولیه
– استفاده از سیستمهای اندازهگیری دقیق
– آموزش اپراتورها
– نگهداری منظم ماشینآلات
– پایش مداوم پارامترهای فرآیند
نکات مهم در مورد تعداد لوبها:
· لوب 3: معمولاً نشاندهنده مشکل در تنظیم زاویه مرکز است
· لوب 4: اغلب به دلیل عدم تطابق سرعتهای دورانی ایجاد میشود
· لوبهای بالاتر (5-9): معمولاً نشاندهنده مشکلات پیچیدهتر مانند ترکیبی از ارتعاشات و تنظیمات نادرست هستند
دیدگاهتان را بنویسید